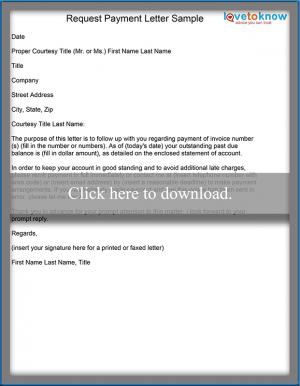
Using the per-hour overhead rate, overhead cost would be applied to each item based on the number of direct labor hours used in producing the good. The traditional method of cost accounting refers to the allocation of manufacturing overhead costs to the products manufactured. If a manufacturer wants to know the true cost to produce specific products for specific customers, the traditional method of cost accounting is inadequate. Activity based costing (ABC) was developed to overcome the shortcomings of the traditional method. Instead of just one cost driver such as machine hours, ABC will use many cost drivers to allocate a manufacturer’s indirect costs.
Both methods estimate overhead costsrelated to productionand then assign these costs to products based on a cost-driver rate. The differences are in the accuracy and complexity of the two methods. Traditional costing is more simplistic and less accurate than ABC, and typically assigns overheadcosts to products based on an arbitrary average rate. This method first assigns indirect costs to activitiesand then assigns the costs to products based on the products’ usage of the activities. As an activity-based costing example, consider Company ABC that has a $50,000 per year electricity bill.
What Are the Two Stages of Allocation in Activity-Based Costing?
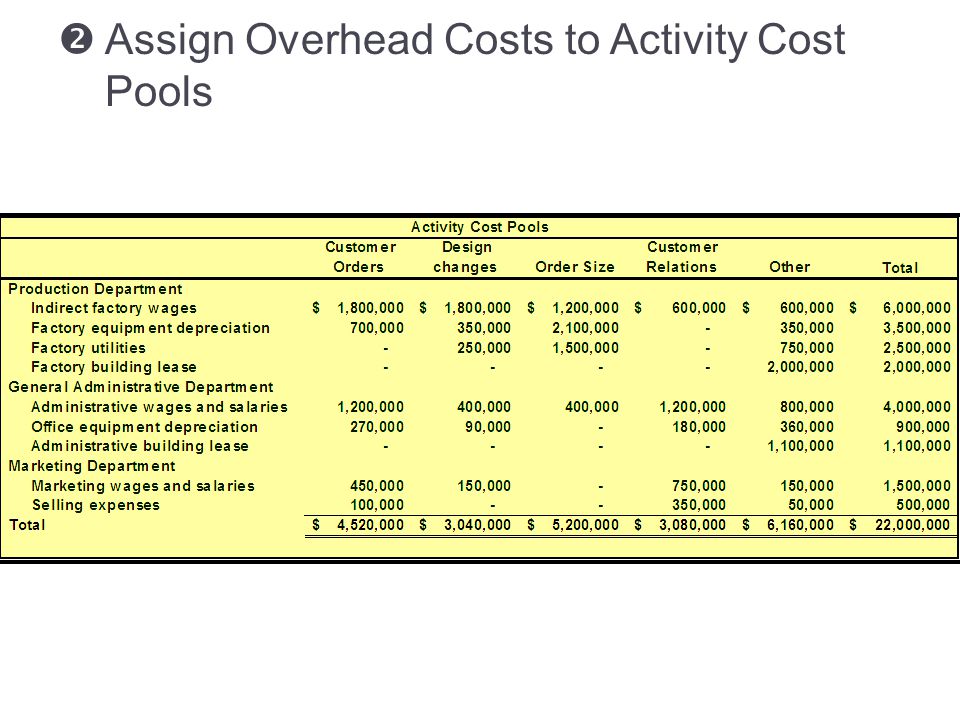
For example, the setup cost for a certain machine in the production area is $50,000 per year. Since this machine is set up 100 times per year, the first stage allocation is to calculate that each machine setup (an activity) is assigned a $500 charge (calculated as the $50,000 setup cost divided by 100 setups). The main costs and limitations of an ABC system are the measurements necessary to implement it.
Generally, the business would try to select a metric that is the underlying cause of overhead costs. For example, a business might choose direct labor hours as the allocation metric. The total overhead expense would be divided by the total number of direct labor hours for the financial period.
Traditional Costing Method
Under activity based costing, $200,000 of the overhead will be viewed as a batch-level cost. This means that $200,000 will first be allocated to batches of products to be manufactured (referred to as a Stage 1 allocation), and then be assigned to the units of product in each batch (referred to as Stage 2 allocation). For example, if Batch X consists of 5,000 units of product, the setup cost per unit is $0.10 ($500 divided by 5,000 units). If Batch Y is 50,000 units, the cost per unit for setup will be $0.01 ($500 divided by 50,000 units). For simplicity, let’s assume that the remaining $1,800,000 of manufacturing overhead is caused by the production activities that correlate with the company’s 100,000 machine hours.
What are the four steps in the cost allocation process?
First stage allocation. A first stage allocation is the process used to assign overhead costs to activities. This allocation is employed in an activity-based costing system, and is the first step in the eventual allocation of overhead costs to cost objects.
Where products use common resources differently, some sort of weighting is needed in the cost allocation process. The cost driver is a factor that creates or drives the cost of the activity. For the activity of running machinery, the driver is likely to be machine operating hours, looking at labor, maintenance, and power cost during the period of machinery activity.
- Generally, the business would try to select a metric that is the underlying cause of overhead costs.
- Activity-based costing is the newest means of calculating how overhead expenses are allocated to different products at the time of publication.
For the year, there were 2,500 labor hours worked, which in this example is the cost driver. Calculating the cost driver rate is done by dividing the $50,000 a year electric bill by the 2,500 hours, yielding a cost driver rate of $20. The formula for activity-based costing is the cost pool total divided by cost driver, which yields the cost driver rate. The cost driver rate is used in activity-based costing to calculate the amount of overhead and indirect costs related to a particular activity. Activity-based costing (ABC) is a costing method that identifies activities in an organization and assigns the cost of each activity to all products and services according to the actual consumption by each.
Activity based costing (ABC) assigns manufacturing overhead costs to products in a more logical manner than the traditional approach of simply allocating costs on the basis of machine hours. Activity based costing first assigns costs to the activities that are the real cause of the overhead. It then assigns the cost of those activities only to the products that are actually demanding the activities.
Activity cost drivers are used in activity-based costing, and they give a more accurate determination of the true cost of business activity by considering the indirect expenses. These levels include batch-level activity, unit-level activity, customer-level activity, organization-sustaining activity, and product-level activity. Activity-based costing benefits the costing process by expanding the number of cost pools that can be used to analyze overhead costs and by making indirect costs traceable to certain activities. Activity-based costing (ABC) is a method of assigning overhead and indirect costs—such as salaries and utilities—to products and services. However, as the percentages of indirect or overhead costs rose, this technique became increasingly inaccurate, because indirect costs were not caused equally by all products.
First stage allocation
This model assigns more indirect costs (overhead) into direct costs compared to conventional costing. A first stage allocation is the process used to assign overhead costs to activities. This allocation is employed in an activity-based costing system, and is the first step in the eventual allocation of overhead costs to cost objects.
Consequently, when multiple products share common costs, there is a danger of one product subsidizing another. ABC provides cost driver rates and information on transaction volumes which are very useful to management for cost management and performance appraisal of responsibility centres. Cost driver rates can be used advantageously for the design of new products or existing products as they indicate overhead costs that are likely to be applied in costing the product. A primary disadvantage of ABC is that it is not possible to divide some overhead costs such as the chief executive’s salary on a per-product usage basis.
Activity-based costing is the newest means of calculating how overhead expenses are allocated to different products at the time of publication. The traditional allocation method requires the business to pick one metric to use as a means to allot overhead costs.
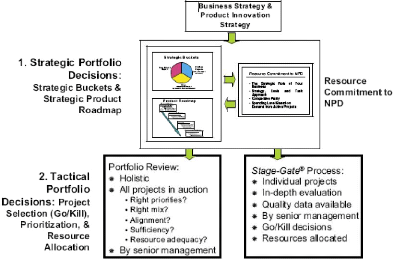
Robin Cooper and Robert S. Kaplan, proponents of the Balanced Scorecard, brought notice to these concepts in a number of articles published in Harvard Business Review beginning in 1988. Cooper and Kaplan described ABC as an approach to solve the problems of traditional cost management systems.
ABC systems require management to estimate costs of activity pools and to identify and measure cost drivers to serve as cost allocation bases. Even basic ABC systems require many calculations to determine costs of products and services.
A few of the cost drivers that would be used under ABC include the number of machine setups, the pounds of material purchased or used, the number of engineering change orders, the number of machine hours, and so on. Activity-based costing (ABC) is a costing method that assigns overhead and indirect costs to related products and services. This accounting method of costing recognizes the relationship between costs, overhead activities, and manufactured products, assigning indirect costs to products less arbitrarily than traditional costing methods. However, some indirect costs, such as management and office staff salaries, are difficult to assign to a product. Direct labour and materials are relatively easy to trace directly to products, but it is more difficult to directly allocate indirect costs to products.
Similarly, employees rarely devote 100% of their working hours to productive activities, and not all productive activities add value to the product or process of the firm. The cost driver rate, which is the cost pool total divided by cost driver, is used to calculate the amount of overhead and indirect costs related to a particular activity. The cost per setup is calculated to be $500 ($200,000 of cost per year divided by 400 setups per year).