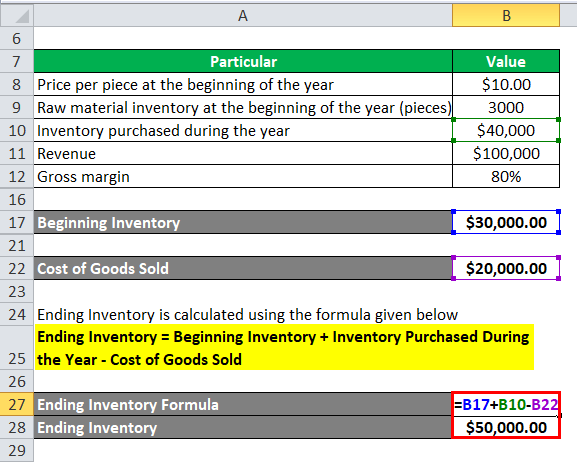
Suppose you have $5,000 of raw materials, buy $5,000 more in the period and use up $4,000. If $2,000 of the remaining materials become obsolete, your ending balance is $4,000, which will be the beginning balance of the next quarter. To get the ending raw materials inventory for an accounting period, you add the beginning balance together with any raw materials purchased. Subtract the materials that were used in manufacturing, whether the goods are finished or still work in progress. This gives you the ending raw materials inventory, which is the beginning inventory for the next period.
Accounting for Raw Materials
As such, the purpose of each seems to be that of maintaining a high level of customer service or part of an attempt to minimize overall costs. When large quantities are ordered or produced, inventory holding costs are increased, but ordering/setup costs decrease. Conversely, when lot sizes decrease, inventory holding/carrying costs decrease, but the cost of ordering/setup increases since more orders/setups are required to meet demand. When the two costs are equal (holding/carrying costs and ordering/setup costs) the total cost (the sum of the two costs) is minimized. Cycle inventories, sometimes called lot-size inventories, result from this process.
It consists of all the component parts that your company hasn’t turned into either finished goods or works in progress. Your raw materials inventory also includes indirect materials, such as lubricants or rags that you use when creating finished goods. Knowing your raw materials inventory is important for accounting and also for business efficiency. Raw materials may sometimes be declared obsolete, possibly because they are no longer used in company products, or because they have degraded while in storage, and so can no longer be used. If so, they are typically charged directly to the cost of goods sold, with an offsetting credit to the raw materials inventory account.
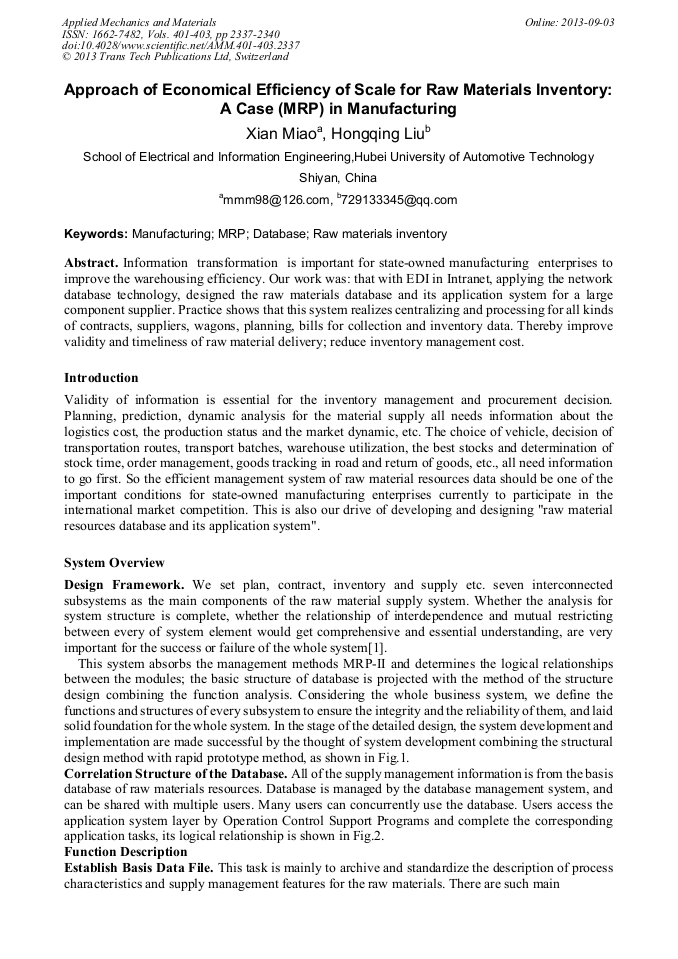
For indirect materials, debit the overhead account and credit the raw materials inventory asset account. At the end of the accounting period, the balance of the overhead account is allocated to the cost of goods sold and ending inventory. For direct materials, debit the work in process inventory account and credit the raw materials inventory account. If the production process is so short that it doesn’t make sense to use a work in process account, debit the finished goods inventory instead. Once the finished goods are sold, the cost of the raw materials should be recorded in the cost of goods sold account.
After this process, she regurgitates the nectar solution into a droplet that hangs from her mouth in the air for as long as 20 minutes to further evaporate moisture. Bees may fan the cells to continue removing moisture from partially filled uncapped cells. Workers will seal cells with a thin layer of wax once the honey moisture content drops to 20%.
The cost of goods flows to the income statement via the Cost of Goods Sold (COGS) account. The calculation also assumes that both ordering and holding costs remain constant.
Economic order quantity (EOQ) is the ideal order quantity a company should purchase to minimize inventory costs such as holding costs, shortage costs, and order costs. This production-scheduling model was developed in 1913 by Ford W. Harris and has been refined over time. The formula assumes that demand, ordering, and holding costs all remain constant. In manufacturing concern, plant and machinery should always keep running.
FINANCE YOUR BUSINESS
How do you find raw materials inventory?
Raw materials inventory is the total cost of all component parts currently in stock that have not yet been used in work-in-process or finished goods production. There are two subcategories of raw materials, which are: Direct materials. These are materials incorporated into the final product.
These are the partly processed raw materials lying on the production floor. It is unavoidable inventory which will be created in almost any manufacturing business.
For that reason, the stock of input for all the machines should be sufficient to keep the factory running. Under normal conditions, a business transports raw materials, WIP, finished goods etc from one site to other for various purpose like sales, purchase, further processing etc. Due to long distances, the inventory stays on the way for days, weeks and even months depending on distances. Once a house bee has received a full load of nectar, which is composed of about 90% water, she manipulates it with her mouthparts to promote moisture evaporation. At the same time she uses enzymes to break down the sugars to more digestible forms and to protect the honey from bacteria during storage.
- For indirect materials, debit the overhead account and credit the raw materials inventory asset account.
- At the end of the accounting period, the balance of the overhead account is allocated to the cost of goods sold and ending inventory.
- For direct materials, debit the work in process inventory account and credit the raw materials inventory account.
They also may be objects or elements that the firm has purchased from outside the organization. Even if the item is partially assembled or is considered a finished good to the supplier, the purchaser may classify it as a raw material if his or her firm had no input into its production. Typically, raw materials are commodities such as ore, grain, minerals, petroleum, chemicals, paper, wood, paint, steel, and food items.
Or, if the production process is brief, bypass the work-in-process account and debit the finished goods inventory account instead. The cost of raw materials on hand as of the balance sheet date appears in the balance sheet as a current asset.
The act of stopping machinery, costs to the entrepreneur in terms of additional set up costs, repairs, idle time depreciation, damages, trial runs etc. In a production line, one machine/process uses the output of other machines/process. The speed of different machines may not always integrate with each other.
Oftentimes, firms will purchase and hold inventory that is in excess of their current need in anticipation of a possible future event. Such events may include a price increase, a seasonal increase in demand, or even an impending labor strike. Therefore, the firm has avoided both excessive overtime due to increased demand and hiring costs due to increased demand. It also has avoided layoff costs associated with production cut-backs, or worse, the idling or shutting down of facilities.
AccountingTools
This process is sometimes called “smoothing” because it smoothes the peaks and valleys in demand, allowing the firm to maintain a constant level of output and a stable workforce. Raw materials are inventory items that are used in the manufacturer’s conversion process to produce components, subassemblies, or finished products. These inventory items may be commodities or extracted materials that the firm or its subsidiary has produced or extracted.
MANAGE YOUR BUSINESS
However, items such as nuts and bolts, ball bearings, key stock, casters, seats, wheels, and even engines may be regarded as raw materials if they are purchased from outside the firm. You calculate and record beginning inventory so that you can calculate ending inventory. If, say, you’re making out your balance sheet, you’ll need to include inventory levels as an asset. It’s acceptable accounting practice to combine raw materials, works in progress and finished goods into a single balance sheet asset account. If this happens, subtract them from the raw inventory account and debit cost of goods sold.
Raw materials may be aggregated into a single inventory line item in the balance sheet that also includes the cost of work-in-process and finished goods inventory. Raw materials inventory is the total cost of all component parts currently in stock that have not yet been used in work-in-process or finished goods production. Higher sales (and thus higher cost of goods sold) leads to draining the inventory account. The conceptual explanation for this is that raw materials, work-in-progress, and finished goods (current assets) are turned into revenue.
Debit the factory overhead account and credit the raw materials inventory asset account. At the end of the month, the ending balance in the overhead account is allocated to the cost of goods sold and ending inventory. Debit the work-in-process inventory account and credit the raw materials inventory asset account.
What is a raw material example?
Add together the initial value of raw materials, works in progress and finished goods to get beginning overall inventory. Add raw materials purchases during the period and subtract the ending inventory balance. That gives you cost of goods sold, which helps determine your income for the period.