The widgets then move to the trimming department for further work, and these per-unit costs will be carried along with the widgets into that department, where additional costs will be added. Process costing is used when there is mass production of similar products, where the costs associated with individual units of output cannot be differentiated from each other.
Example of Process Costing
Manufacturing companies need to know how much it costs to manufacture a product in order to set their sales price and determine if it’s producing a profit. Product costing is the process of determining the business expenses associated with the manufacture of a product.
When dissimilar products are manufactured by the same company, job costing techniques are used. These techniques determine the products’ cost drivers, or activities that control the amount of costs incurred, then allocate expenses by dividing the expenses by their associated drivers.
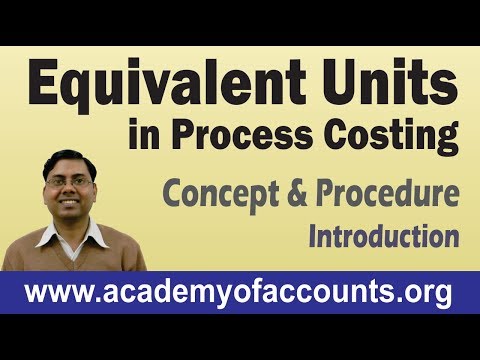
Inventory Accounts Similarities Inventory accounts include raw materials inventory, work-in-process inventory, and finished goods inventory. Differences Process Costing Job Costing Several different work-in-process inventory accounts are used—one for each department (or process). One work-in-process inventory account is used—job cost sheets track costs assigned to each job.
In other words, the cost of each product produced is assumed to be the same as the cost of every other product. Under this concept, costs are accumulated over a fixed period of time, summarized, and then allocated to all of the units produced during that period of time on a consistent basis.
Management accountants may also leave out production costs and create under-costed products. Under-costed products usually result in lower business profits because goods are actually more expensive than actually reported.
However, job costing does not work for manufacturing companies that produce products that are identical, or very similar, such as food or oil, because each unit costs the same to produce. Process costing systems allocate expenses to products by adding total costs at each stage of the manufacturing process then dividing these costs by the total number of units produced. This enables these companies to determine the costs associated with the products at each stage of the manufacturing process and cut costs as necessary per stage of manufacture. Process costing is an easier system to use when costing homogenous products compared to other cost allocation methods.
Process costing may allow non-production costs to be included in the total process cost. Including non-production costs will arbitrarily increase each item’s cost; this also increases the consumer product price.
What is an example of process costing?
Process costing is a term used in cost accounting to describe one method for collecting and assigning manufacturing costs to the units produced. A processing cost system is used when nearly identical units are mass produced.
- Process costing can create cost errors in the production system.
- Production cost errors often represent a significant disadvantage for cost accounting systems.
- Process costing does not use direct allocation to apply business costs to individual goods.
The importance of process costing
Differences Process Costing Job Costing Product costs are assigned to departments (or processes). Unit Cost Information Similarities Unit cost information is needed by management for decision-making purposes. Differences Process Costing Job Costing Unit cost information comes from the departmental production cost report.
Process costing can create cost errors in the production system. Production cost errors often represent a significant disadvantage for cost accounting systems. Process costing does not use direct allocation to apply business costs to individual goods. Direct allocation costing applies a specific amount of raw materials, production labor and manufacturing overhead to goods or services.
Cost accounting utilizes either job costing, process costing, or a hybrid of both. In this article, we will discuss the differences between job costing and process costing as well as advantages or disadvantages of each. As a process costing example, ABC International produces purple widgets, which require processing through multiple production departments. The first department in the process is the casting department, where the widgets are initially created. During the month of March, the casting department incurs $50,000 of direct material costs and $120,000 of conversion costs (comprised of direct labor and factory overhead).
Business owners allocate business costs according to the number of processes each good travels through in the production system. Each process applies direct materials, labor and manufacturing overhead to the production cost total. Management accountants take the total number of goods leaving the process and divide the total process cost by this number.
Cost accounting helps managers determine the costs of running a business by recording the costs of materials, processes, and projects. Analyzing trends on costs of production and overhead along with revenue helps management make informed decisions on how to improve, scale, or grow effectively.
Process costing
If a process costing system does not mesh well with a company’s cost accounting systems, there are two other systems available that may be a better fit. The job costing system is designed to accumulate costs for either individual units or for small production batches. Product Costs Similarities Product costs consist of direct materials, direct labor, and manufacturing overhead.
Accounting for Managers
When products are instead being manufactured on an individual basis, job costing is used to accumulate costs and assign the costs to products. When a production process contains some mass manufacturing and some customized elements, then a hybrid costing system is used.
This creates a simple average cost for each item produced. Direct materials are materials that are consumed during the manufacture of a product. To determine the cost per unit under process costing, each expense must first be assigned to a process then categorized as a direct materials cost or conversion cost. Once these steps have been completed, the expenses can be divided by total units produced to obtain the cost per unit.