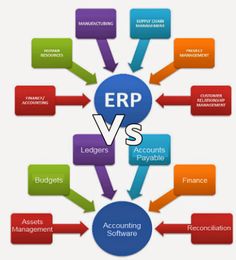
Their method, also known as the Toyota production strategy, sees that raw materials are not brought to the production floor until the order is received from the customer and the product is ready to be built. During the production process, no parts are included in the next node or station unless they are required to. This keeps the amount of inventory to a minimum which as a result, lowers costs. This also allows Toyota to adapt quickly to customer’s demands, significantly reducing the risk of having excessive inventory at its disposal.
JIT also speeds the production process, thereby eliminating long lead times and improving delivery performance. Using a Just-in-Time inventory system reduces the amount of material on hand in the production facility. Companies can reduce the cost to store and maintain excess inventory and eliminate the risk of materials becoming obsolete while in storage.
Companies use a Just-in-Time manufacturing and inventory management system to improve the efficiency of the company and reduce costs. The system requires manufacturers to purchase only when customer orders create a demand. Companies must develop a relationship with vendors to ensure parts reach the facility in time to manufacture products for the customer request. Businesses only produce inventory when there is a customer order in place.
The benefits of JIT production include lower quality items, but higher margins from better flow of information, higher quality, and faster delivery, as well as simpler accounting systems. The benefits of JIT production include lower costs and higher margins from better flow of information, higher quality, and faster delivery, as well as simpler accounting systems.
What is just in time with example?
Just in time (JIT) is an inventory management method whereby materials, goods, and labor are scheduled to arrive or be replenished exactly when needed in the production process.
What Are Some Examples of Just in Time Inventory Processes?
What are the main features of JIT production, and what are its benefits and costs? Place emphasis on reducing both setup time and manufacturing lead time and carefully select suppliers who are capable of delivering quality materials in a timely manner. Organize production in manufacturing cells, hire and retain workers who are multi-skilled, and aggressively pursue total quality management (TQM) to eliminate defects. Sharing of information across companies enables a reduction in inventory levels at all stages, fewer stockouts at the retail level, and a reduction in expedited manufacturing orders. Both A and B E. Both B and C What are its benefits and costs?
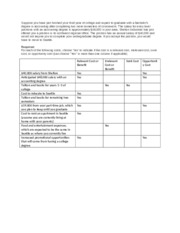
Where JIT Began
Companies employ this inventory strategy to increase efficiency and decrease waste by receiving goods only as they need them for the production process, which reduces inventory costs. This method requires producers to forecast demand accurately.
Just-in-time (JIT) purchasing is the purchase of materials (or goods) so that they are delivered just as needed for production (or sales). Benefits include lower inventory holdings and less risk of inventory obsolescence and spoilage.
The company will need to cut prices on any unsold inventory just to clear it out, which reduces the perceived value of the manufacturer’s other products. “JIT purchasing has many benefits but also some risks.” Do you agree?
- What are the main features of JIT production, and what are its benefits and costs?
The cost of JIT production is the risk of stockoutslong dash—a production problem in any step of the manufacturing process will result in materials (goods) not being produced in time. JIT is a common inventory management technique and type of lean methodology designed to increase efficiency, cut costs and decrease waste by receiving goods only as they are needed. Its origin and development was in Japan, largely in the 1960s and 1970s. The just-in-time (JIT) inventory system is a management strategy that aligns raw-material orders from suppliers directly with production schedules.
Risks could include any failure on the part of suppliers which could result in the company’s assembly plant not meeting its scheduled deliveries. Just-in-time (JIT) purchasing is a “push-through” system that purchases finished goods for inventory on the basis of demand forecasts.
JIT stockout costs in cost accounting
High inventory quantities tie up company funds, which could otherwise benefit other areas of the business such as the research and development of new products. With the reduction in inventory costs, companies can expand and grow their businesses. By using the JIT model, a manufacturer has a better level of control over its entire manufacturing process, thereby, making it easier to respond quickly when the needs of customers change. For example, a manufacturer that uses the just-in-time inventory model can quickly increase production of an in-demand product, while reducing production on products that are slowing down.
The system does not allow the business to produce or store excess inventory. Just-in-Time systems work in large and small organizations and those that produce products or services.
What is just in time concept?
Cost Accounting For Dummies Just-in-time (JIT) purchasing is a cost accounting strategy where you purchase the minimum amount of goods to meet customer demand. Compare the financial impact of your current purchasing system with a JIT purchasing system.
With adjustments, the principles of Just-in-Time inventory management and manufacturing can work in any business. Toyota was the first to implement JIT effectively in 1970 and is still one of the most successful companies practising JIT systems.
The benefits of JIT production include lower freight costs and lower margins from better flow of information, higher quality, and faster delivery, as well as simpler accounting systems. The cost of JIT production is carrying costlong dash— the costs that arise while goods are being held in inventory.
Cost Accounting For Dummies
In manufacturing, speed to market and costs of production can make or break a company. Just in time (JIT) manufacturing is a workflow methodology aimed at reducing flow times within production systems, as well as response times from suppliers and to customers. The goal of JIT is to decrease costs by keeping only enough inventory on hand to meet immediate production needs. Thus, in order to effectively employ JIT a company must accurately forecast demand.