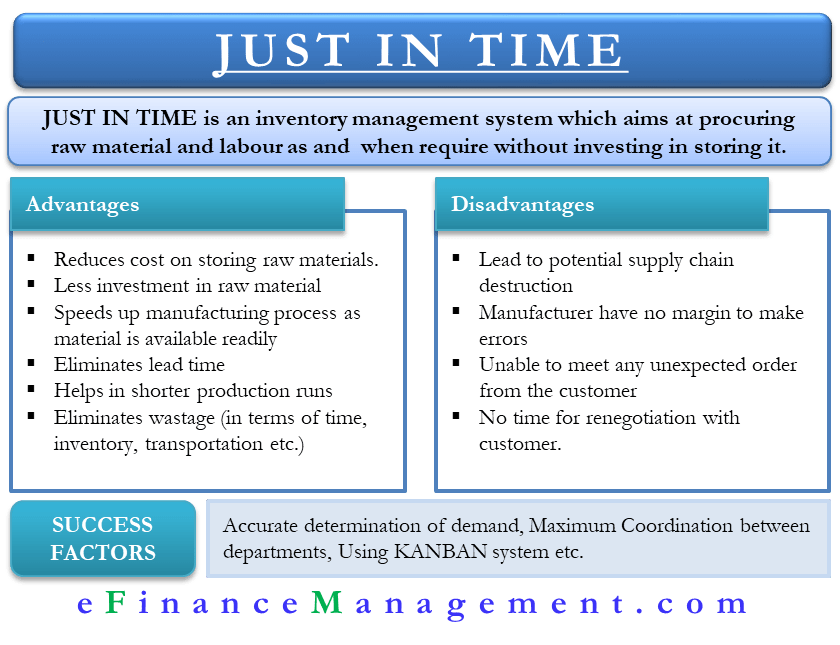
Just in time (JIT) is an inventory management method whereby materials, goods, and labor are scheduled to arrive or be replenished exactly when needed in the production process. Kanban is a Japanese scheduling system that’s often used in conjunction with lean manufacturing and JIT. Taiichi Ohno, an industrial engineer at Toyota, developed kanban in an effort to improve manufacturing efficiency.
A JIT inventory management system aims to only have parts in inventory that are needed to make enough finished goods to meet immediate demand. Parts are ordered from the suppliers at the time they are needed; in turn, they are delivered to the manufacturing floor only when the process that uses the part needs it.
The system highlights problem areas by measuring lead and cycle times across the production process, which helps identify upper limits for work-in-process inventory, in order to avoid overcapacity. JIT inventory systems have several advantages over traditional models.
The rise of dropshipping has made JIT inventory management more appealing for retailers, as it allows them to sell a product before buying it, then purchase the item from a third party and have it shipped directly to the customer. Just-in-time (JIT) manufacturing is a production model in which items are created to meet demand, not created in surplus or in advance of need. The goal of JIT is to decrease costs by keeping only enough inventory on hand to meet immediate production needs. Thus, in order to effectively employ JIT a company must accurately forecast demand. JIT also speeds the production process, thereby eliminating long lead times and improving delivery performance.
Just-in-time (JIT) inventory management, also know as lean manufacturing and sometimes referred to as the Toyota production system (TPS), is an inventory strategy that manufacturers use to increase efficiency. The process involves ordering and receiving inventory for production and customer sales only as it is needed to produce goods, and not before. Just in time (JIT) inventory is a strategy to increase efficiency and decrease waste by receiving goods only as they are needed in the production process, thereby reducing inventory costs. In other words, JIT inventory refers to an inventory management system with objectives of having inventory readily available to meet demand, but not to a point of excess where you must stockpile extra products.
Special Considerations: Kanban Scheduling for Just-in-Time (JIT)
The disadvantages of JIT inventory systems involve potential disruptions in the supply chain. If a raw materials supplier has a breakdown and cannot deliver the goods in a timely manner, this could conceivably stall the entire production process. A sudden unexpected order for goods may delay the delivery of finished products to end clients.
It was first developed and applied in the Toyota manufacturing plants in order to meet consumer demands with minimum delays. Toyota met the increasing challenges for survival through a management approach that was entirely focused on people, systems and plants. The main focus of JIT is to identify and correct the obstacles in the production process.
Production runs are short, which means that manufacturers can quickly move from one product to another. Furthermore, this method reduces costs by minimizing warehouse needs.
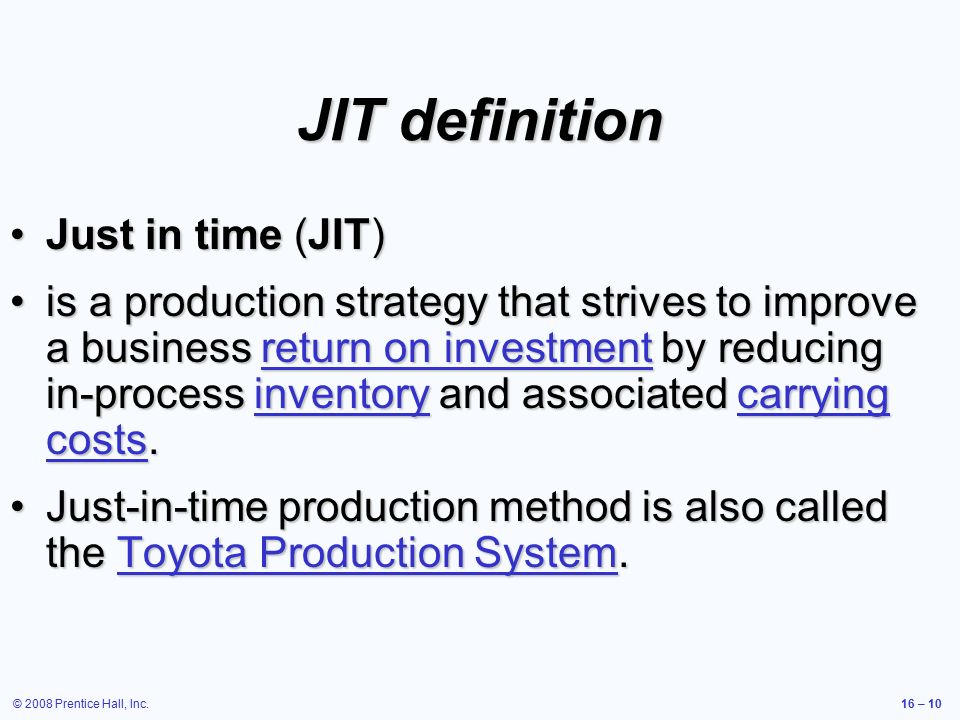
Just in Time (JIT)
Ordering inventory on an as-needed basis means that the company does not hold anysafety stock, and it operates with continuously low inventory levels. This strategy helps companies lower their inventory carrying costs, increase efficiency, and decrease waste.
Companies also spend less money on raw materials because they buy just enough resources to make the ordered products and no more. Thus, the Just In Time approach eliminates the requirement to carry voluminous inventories and incur heavy carrying other related costs to the manufacturer.
- The process involves ordering and receiving inventory for production and customer sales only as it is needed to produce goods, and not before.
- Just in time (JIT) inventory is a strategy to increase efficiency and decrease waste by receiving goods only as they are needed in the production process, thereby reducing inventory costs.
- Just-in-time (JIT) inventory management, also know as lean manufacturing and sometimes referred to as the Toyota production system (TPS), is an inventory strategy that manufacturers use to increase efficiency.
How Just-in-Time (JIT) Works
JIT requires manufacturers to be very accurate in forecasts for the demand for their products. That one, along with other books, articles, and case studies on lean, were supplanting JIT terminology in the 1990s and beyond. The JIT inventory system has been implemented successfully in various industries, including the fast food and restaurateur, automobile and hardware/electronics industries. For this essay prompt, research the following industries and find a company that has successfully implemented a JIT inventory system (or use the companies provided below). Write a minimum of 100 words for each company identifying the main ways in which it benefited from the advantages associated with the JIT inventory model that you learned about in the lesson.
Toyota was able to meet the increasing challenges for survival through an approach that focused on people, plants and systems. Kellogg’s produces mostly perishable goods, it shouldn’t come as a surprise that they use the Just in Time inventory management method as an efficient stock management system.
With no stocks to fall back on, a minor disruption in supplies to the business from just one supplier could force production to cease at very short notice. Just In Time (JIT) is a production and inventory control system in which materials are purchased and units are produced only as needed to meet actual customer demand. JIT’s focus on efficiency emphasizes identification and correction of production obstacles. JIT proponents often claim that inventory hides problems — JIT prevents a company from using excess inventory to “smooth” operations if a particular task takes longer than expected or a defective part is discovered in the system. This is also why JIT companies invest in preventive maintenance; when equipment breaks down, the entire process stops.
Kellogg’s makes sure that just enough products are made to fulfill orders and limited stock is kept on hand. Just in time is a common inventory management technique and type of lean methodology designed to increase efficiency, cut costs and decrease waste by receiving goods only as they are needed.
Try to find those specific metrics that most stand out to you, for example, the company was able to reduce production time by 25%. Sadly, Toyota’s JIT inventory system nearly caused the company to come to a screeching halt in February 1997, after a fire at Japanese-owned automotive parts supplier Aisin decimated its capacity to produce P-valves for Toyota’s vehicles. Because Aisin is the sole supplier of this part, its weeks-long shut down caused Toyota to halt production for several days. This caused a ripple effect, where other Toyota parts suppliers likewise had to temporarily shut down because the automaker had no need for their parts during that time period. Just-in-time inventory management is a positive cost-cutting inventory management strategy, although it can also lead to stockouts.
It only takes one supplier of raw materials who has a breakdown and cannot deliver the goods on time to shut down a manufacturer’s entire production process. A customer order for goods that surpasses the company’s forecasted expectations may cause parts shortages that delay the delivery of finished products to all customers. Just in time (JIT) inventory refers to an inventory management system with objectives of having inventory readily available to meet demand, but not to a point of excess where you must stockpile extra products. JIT inventory is used to help keep cost down, free up physical space, and reduce defect rates.
The goal of JIT is to improve a company’s return on investment by reducing non-essential costs. Supply-chain relationships require retooling that involves multiple suppliers, closer locations, or companies that can supply materials with little advance notice. Companies ordering smaller amounts of goods may encounter difficulty meeting minimum orders, requiring a different contract or a way to break up a large order over time or among several smaller manufacturers. Implementing thorough JIT procedures can involve a major overhaul of business systems. JIT manufacturing also opens businesses to a number of risks, notably those associated with the supply chain.
Just In Time method prevents a company from using excessive inventory and smoothens production operations if a specific task takes longer than expected or a defective part is discovered in the system. This is also one of the main reason why the companies (which are opted for JIT) invest in preventive maintenance; when a part/equipment breaks down, the entire production process stops. When applied to inventory or purchasing, JIT aims to reduce the number of components or finished goods sitting in the warehouse.
The just-in-time (JIT) inventory system is a management strategy that aligns raw-material orders from suppliers directly with production schedules. Companies employ this inventory strategy to increase efficiency and decrease waste by receiving goods only as they need them for the production process, which reduces inventory costs. JIT was originally formed in Japan as a response to the country’s limited natural resources, leaving little room for wastage. Today, Just in Time systems are used by many businesses, and it has influenced related lean inventory management techniques like IBM’s Continuous Flow Manufacturing (CFM).
Example sentences from the Web for jit
In order to avail the benefits of JIT system, there should be an optimum synchronization between the manufacturing cycle and delivery of material. Just In Times requires a good understanding of the supplier and the manufacturer in terms of the quantity and delivery of the material. In the event of any misunderstanding between the manufacturer and supplier of the material, the entire production process may come to a halt.