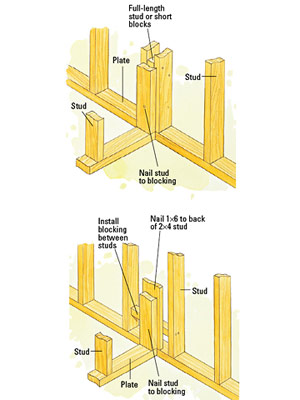
It’s rare for an organization to use a single type of maintenance. Even a state of the art manufacturing plant that has predictive maintenance technology will use less advanced types of maintenance.
Non-routine maintenance includes maintenance that is performed reactively or only when needed based on an asset’s conditions. Scheduled maintenance includes work that is scheduled on a calendar for completion. The most common type of scheduled maintenance is calendar-based preventive maintenance tasks.
This may involve bringing performance levels up to their original level from when an asset was originally acquired, or merely maintaining the current performance level of an asset. Expenditures required to increase the performance level may result in the capitalization of the additional costs. For example, replacing the oil filter in a truck is considered a maintenance cost, while replacing the roof of a building extends the life of the building, and so its cost will be capitalized.
Preventive maintenance is carried out to avoid breakdown of machinery and occurrence of maintenance problems in buildings and services. Works of preventive maintenance are carried out on the basis of regular inspection survey. Emergency maintenance occurs when an asset requires immediate attention in order to keep a facility operational or safe.
The guidelines are pretty straightforward and we outline the process below. Building repairs and maintenance services mainly includes works undertaken for maintaining proper condition of buildings, its services and works in ordinary use. The use for which buildings are designed is the main factor in determining the required standard of maintenance. Routine maintenance is a form of time-based maintenance and preventive maintenance, though some organizations differentiate between routine maintenance and preventive maintenance. Additionally, routine maintenance is performed by operators, janitors, and other staff member while preventive maintenance is performed by technicians.
This is not the case with predictive maintenance which requires condition monitoring sensors and new software integrations. However, with preventive maintenance, the organization runs the risk of over-scheduling maintenance tasks because tasks are scheduled based on time rather than actual conditions. That said, preventive maintenance achieves 12% to 18% cost savings over reactive maintenance. Capital expenditures are costs that a company incurs to purchase an asset, extend its life, or increase its capacity or efficiency. Repairs and maintenance expenses only maintain an asset’s life or current condition.
Words nearby repair
Preventive maintenance is the most popular type of proactive maintenance. To start conducting preventive maintenance tasks (PMs), an organization does not need to purchase new technology if it already has a CMMS.
Small property solutions are good for leased situations. Outsourcing building maintenance tasks is very common.
You may be able to claim capital works deductions for these expenses; for more information see Capital works deductions. For more information, see Guide to capital gains tax.
Explore Dictionary.com
What does it mean to repair something?
Verb (1) mend, repair, patch, rebuild mean to put into good order something that is injured, damaged, or defective. mend implies making whole or sound something broken, torn, or injured.
Condition-based maintenance (CBM) is at the core of predictive maintenance but, on its own, does not rely on technology to determine the condition of an asset like PdM does. For instance, a manager may instruct an operator to monitor the condition of an asset and submit a work request when a specific condition is met. This approach may, or may not be, as reliable as predictive maintenance. An organization that has highly-trained operators may spot hazardous conditions better than an organization using PdM technology that doesn’t know what to look for.
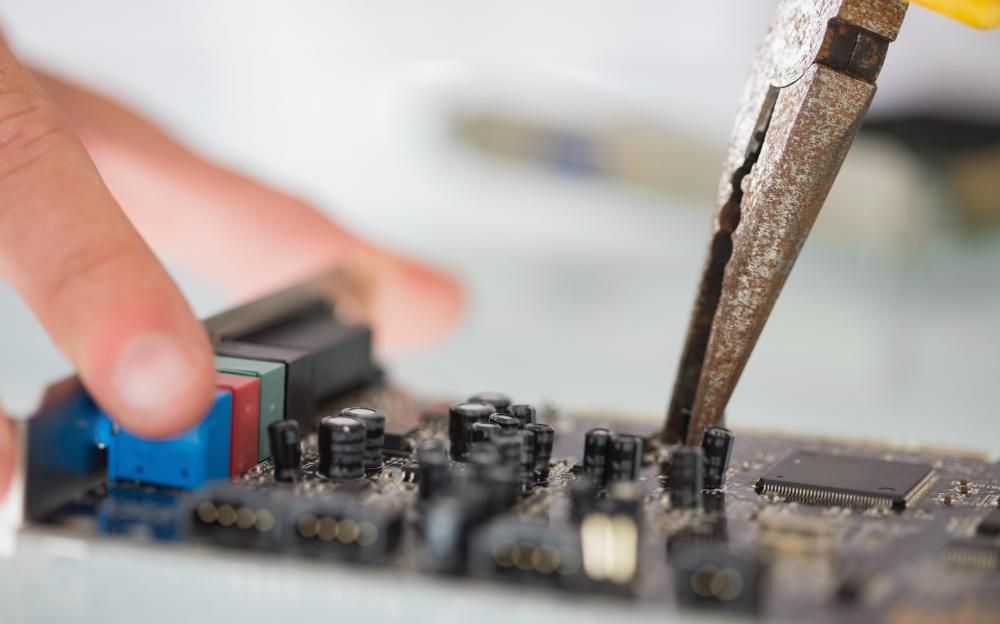
British Dictionary definitions for repairing (1 of
- Preventive maintenance is the most popular type of proactive maintenance.
Deferred maintenance includes repairs and inspections that are put into a backlog due to limited budget and resources. While deferring maintenance saves money up front, the costs of not performing important maintenance compounds at 7% annually. Rising costs come from fines resulting from missed inspections and unscheduled downtime that brings production to a standstill. By far, deferred maintenance and emergency maintenance are the least desired types of maintenance. Repairs and maintenance expense is the cost incurred to ensure that an asset continues to operate.
This is the most reactive and intrusive type of maintenance as it pulls technicians away from other jobs and lowers schedule compliance. In extreme circumstances, emergency maintenance can set an organization back days depending on the scope of the repair, available parts, and the asset’s level of importance. To reduce the amount of emergency maintenance that is both unplanned and unscheduled, organizations adopt various forms of proactive maintenance. Planned maintenance is work that’s prepared for in advance of it taking place.
SYNONYMS FOR repair
Predictive maintenance (PdM) is what savvy maintenance teams aspire to have or are already implementing. The major barrier to PdM is the time it takes to implement rather than the cost of the technology itself. For instance, a vibration sensor that can identify imbalance, misalignment, and resonance issues only costs around $200. But the time it takes to install, integrate with other maintenance software, and adopt a culture around is not time that all organizations are willing to allocate. For those that do allocate the time, PdM provides an 8% to 12% cost savings over preventive maintenance.
The distinction is generally clear, although there are times when a judgement call is needed for a particular expense. Repairs and maintenance are expenses a business incurs to restore an asset to a previous operating condition or to keep an asset in its current operating condition. They are distinct from capital expenses used to purchase the asset.
According to an UpKeep survey, it’s also the most popular key performance indicator (KPI) to track. A high planned maintenance percentage indicates that a maintenance team will have resources available to complete work for the time/day the work is scheduled for. Having a high planned maintenance percentage also helps boost other maintenance KPIs like schedule compliance. More planned maintenance means more successful completion of scheduled maintenance.
The main goal is to manage a building and its grounds, as well as customize needs for the facility. It can include everything from leaky faucets to major repairs. Special repairs of building are undertaken to replace the existing parts of buildings and services which get deteriorated on ageing of buildings.
Write “Repairs and maintenance expense” and the total amount as a line item in the operating expenses section of your income statement. For example, replacing a broken part on an engine is a repair expense, while upgrading the engine to increase a machine’s capacity is a capital expenditure. A company expenses an entire repair or maintenance expense at one time, but allocates a capital expenditure as an expense over time. The purpose of this maintenance service is to ensure satisfactory continuous functioning of various services in the buildings. At the same time, building maintenance should ensure safety to the occupant or the public and should comply with the statutory requirements.
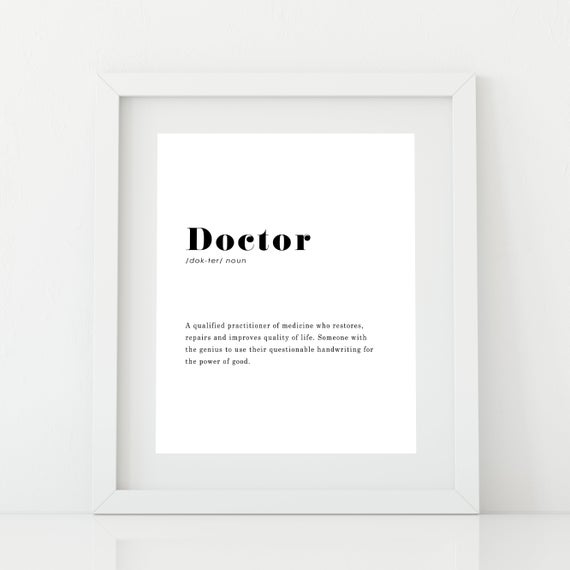
Building maintenance companies seek to develop long term relationships with clients, as well as an environment that is clean, safe, and an enhancement to employees’ work day. One of the greatest challenges is attracting new clients and retain them. That is where superior customer service comes into play. A good building maintenance company will focus on creating trust, as well as showing integrity and high performance. Building maintenance is responsible for a property’s upkeep, including structural, electrical, and plumbing systems.
For instance, an asset with a monthly PM has twelve instances of scheduled maintenance in a given year. However, just because maintenance is scheduled does not mean it’s planned. Some businesses will have daily needs but also have periodic maintenance needs.
repair
It is necessary to prevent the structure & services from deterioration and restore it back to its original conditions to the extent possible. Day to day repairs include service repairs which arises from time to time in the services of the buildings such as in plumbing works, water supply, etc.
What is example of repair?
Repair is the act of fixing or the state of being repaired. An example of a repair is a fixed brake system on a car.
Repairs generally involve a replacement or renewal of a worn out or broken part, for example, replacing worn or damaged curtains, blinds or carpets between tenants. Maintenance generally involves keeping the property in a tenantable condition, for example repainting faded or damaged interior walls. bridges, are entrusted with the care and management of the property and business of the county, and may borrow or raise by tax what is necessary to meet the more common expenses of the county. For example, if you had $10,000 in repairs and maintenance expenses during the year, write “Repairs and maintenance expense $10,000” in the operating expenses section of your income statement. At the end of an accounting period, add up the total repairs and maintenance expenses you have recorded during the period.