Sometimes it is found that one product is of major importance and the others are of minor importance. In such situations products of lesser importance are known as by-products.
If the entity incurs any costs after the split-off point, the costs are likely associated with a specific product, and so can be more readily assigned to them. All the joint products are priced equally when it comes to their economic value. They also share production costs up to the split-off point, which is called the joint cost, after which individual further processing costs are added to the products.
Although both the terms, “common cost” and “joint cost” are sometimes used interchangeably, they differ from each other. Joint costs emerge when multiple products are manufactured in a common process and when common inputs are used.
These products incur undifferentiated joint costs until a split-off point, after which each product incurs separate processing. Prior to the split-off point, costs can only be allocated to the joint products. For example, suppose your retail business pays an annual building rent of $200,000, which is a fixed cost (unless the rental contract with the landlord also has a rent escalation clause based on your sales revenue).
The multiple products have a definite quantitative relationship to each other and the production of one product influences the output of the other product, though in a lesser proportion. Common costs are not the result of any manufacturing compulsion or the use of any single raw material. Joint costs arise where the processing of a single raw material or production resources results in two or more different products simultaneously. Sometimes, joint costs and common costs are used having identical meaning. Joint costs relate to a situation in which the factors of production by their basic nature result in two or more products.
Joint products vs. co-products
There may even be several split-off points; at each one, another product can be clearly identified, and is physically split away from the production process, possibly to be further refined into a finished product. If the company has incurred any manufacturing costs prior to the split-off point, it must designate a method for allocating these costs to the final products.
But the apportionment of joint costs involves many complexities and difficulties in cost accounting. The incurrence of common costs are influenced by management decisions, But joint costs are influenced by common production process and use of common raw materials. Common costs are not only common to products, but they may be common to processes, functions, responsibilities, customers, sales territories, periods of time and similar costing units. For example, the salary of a manager of a production department which is manufacturing three products is an example of common cost with respect to the products.
Joint products – What are joint products?
The rent, which gives the business the legal right to occupy the building, provides 15,000 square feet of retail and storage space. Besides common costs can be apportioned to costing objects like products, jobs, department, etc. without much difficulty.
Joint product:
If the end user of the product is the consumer, then the product is a consumer product. If the end user is a business, then it is categorized as a business product. For example, a stapler can be either, depending on who is using the product. A business product is used to manufacture other goods or services to resell, while a consumer product is purchased to satisfy individual wants or needs. Remember that a product includes all items, such as warranties, packaging, after-sales follow-up material, etc.
- If the end user of the product is the consumer, then the product is a consumer product.
- If the end user is a business, then it is categorized as a business product.
By-products arise out of the scrap of a given production process since there is no intention to create a by-product. Joint products are two or more products that are generated within a single production process; they cannot be produced separately and incur undifferentiated joint costs. Joint products are multiple products generated by a single production process at the same time.
Similarly, the rent of the factory is common to all departments located in the factory. The basic point is that a particular (common) cost may be direct to one object and common as far as other objects are concerned.
For example, if all you want is a Harley-Davidson motorcycle, you’re not going to make any exceptions. Examples of specialty products would also be BMWs, Rolex watches, and Tiffany jewelry. Marketers promote these products to a small target market through limited distribution channels to add to the exclusiveness of the product. A convenience product is a consumer product that takes little thought, is routine, purchased often, appeals to a large target market, and the consumer purchases with little planning. He finds the closest convenience store and rushes in and picks up his favorite Ninja Energy Bar for one dollar.
Consumer products can also be further broken down into specific categories, such as convenience, shopping, specialty, and unsought. For example, kerosene, fuel oil, gasolene and other oil products are derived from crude oil.
Which is an example of joint products?
Joint products are multiple products generated by a single production process at the same time. These products incur undifferentiated joint costs until a split-off point, after which each product incurs separate processing. Prior to the split-off point, costs can only be allocated to the joint products.
By-products are sold at a lower net realizable value or at scrap value. In this lesson, you will learn the difference between business and consumer products. We will also discuss the different ways they can be classified, which include the areas of convenience, shopping, specialty and unsought. A main product is a joint output that generates a significant portion of the net realizable value (NRV) within a joint production process.
Some brands may market their dog food without animal by-products because they don’t contain what consumers think of as by-products (feathers, hair, hooves, etc.). Others may formulate their dog food without these nutrient-dense co-products. The costs allocated to joint products and by-products should have no bearing on the pricing of these products, since the costs have no relationship to the value of the items sold. Prior to the split-off point, all costs incurred are sunk costs, and as such have no bearing on any future decisions – such as the price of a product. Joint products are manufactured using raw materials from the first step.
Because they are deemed to have no influence on reported financial results, by-products do not receive allocations of joint costs. By-products also, by convention, are not inventoried, but the NRV from by-products is typically recognized as “other income”, or as a reduction of joint production processing costs when the by-product is produced.
Add up all production costs through the split-off point, then determine the sales value of all joint products as of the same split-off point, and then assign the costs based on the sales values. If there are any by-products, do not allocate any costs to them; instead, charge the proceeds from their sale against the cost of goods sold. A joint cost is a cost that benefits more than one product, while a by-product is a product that is a minor result of a production process and which has minor sales. Joint costing or by-product costing are used when a business has a production process from which final products are split off during a later stage of production. The point at which the business can determine the final product is called the split-off point.
The jointness results from there being more than one product, and these multi-products are the result of the method of production or the nature of raw material and not of a decision by management to produce both. Although consumption rates of a specialty product can be similar to a shopping product, the price is usually higher and consumers are much more selective in their purchasing. The timing of the purchase might correspond to when they can actually get a fair price.
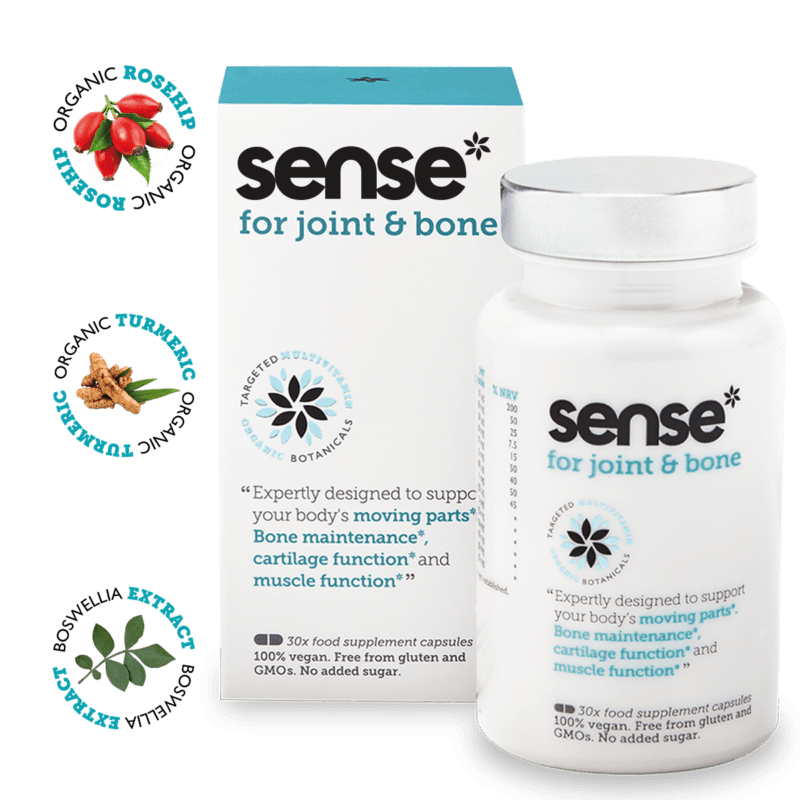
The classification of a product resulting from a joint production process as either a main product or a by-product has relevance in the context of cost management because costs are only allocated to main products, not to by-products. In the context of production, a by-product is the “output from a joint production process that is minor in quantity and/or net realizable value (NRV) when compared with the main products”.
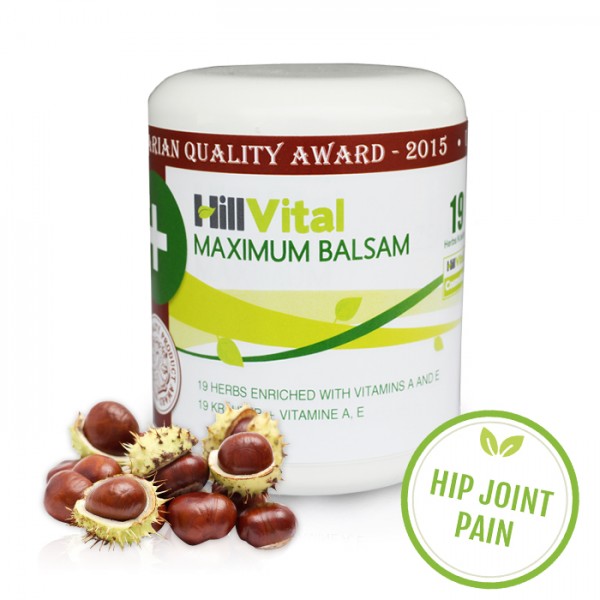