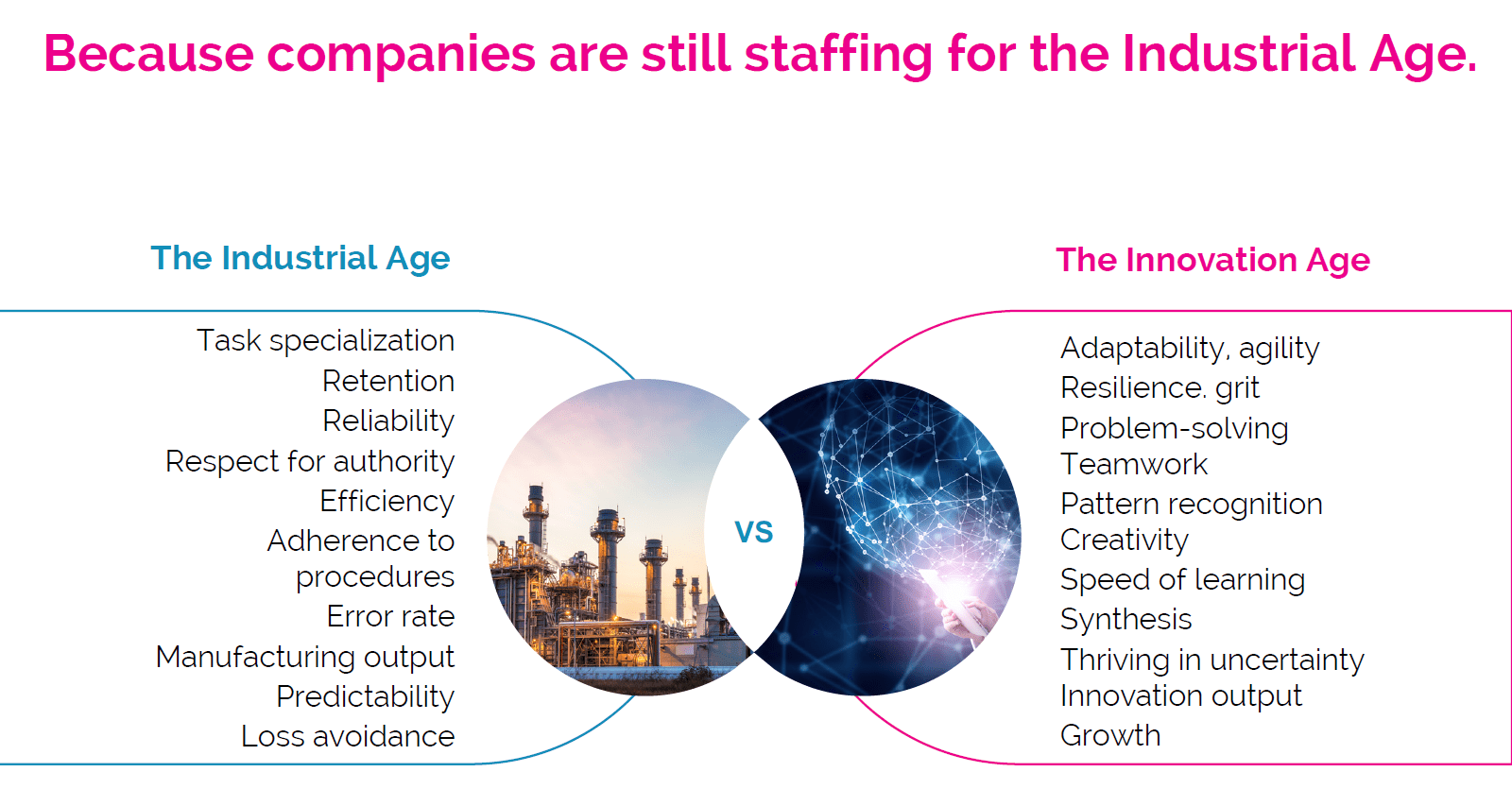
Activity‐based costing assumes that the steps or activities that must be followed to manufacture a product are what determine the overhead costs incurred. Each overhead cost, whether variable or fixed, is assigned to a category of costs. Cost drivers are the actual activities that cause the total cost in an activity cost pool to increase.
Activity-Based Costing Activities
Activity-based costing (ABC) is a costing method that assigns overhead and indirect costs to related products and services. This accounting method of costing recognizes the relationship between costs, overhead activities, and manufactured products, assigning indirect costs to products less arbitrarily than traditional costing methods. However, some indirect costs, such as management and office staff salaries, are difficult to assign to a product. Traditional costing systems allocate manufacturing overhead by dividing total indirect costs by a cost driver to obtain one rate to be used to allocate overhead to different products. Activity-based costing focuses on identifying the activities required to make products, on forming cost pools for each activity, and on allocating overhead costs to the products based on their use of each activity.
The ABC column represents overhead costs allocated using the activity-based costing shown back in Figure 3.5 “Allocation of Overhead Costs to Products at SailRite Company”. This is done by dividing the estimated overhead costs (from step 2) by the estimated level of cost driver activity (from step 3). Figure 3.4 “Predetermined Overhead Rates for SailRite Company” provides the overhead rate calculations for SailRite Company based on the information shown in the previous three steps. As an activity-based costing example, consider Company ABC that has a $50,000 per year electricity bill. The number of labor hours has a direct impact on the electric bill.
A cost driver is an activity that controls the amount of costs incurred. This is the same cost figure used for the plantwide and department allocation methods we discussed earlier. Activity-based costing simply provides a more refined way to allocate the same overhead costs to products. A survey of 130 U.S. manufacturing companies yielded some interesting results. The companies that used activity-based costing (ABC) had higher overhead costs as a percent of total product costs than companies that used traditional costing.
Which is an example of a unit level activity?
Organization-sustaining activities are those actions taken to maintain the operations of a business. For example, a company must pay property taxes, utilities, and insurance, irrespective of what it does to produce goods for sale or provide services to customers.
For the activity of running machinery, the driver is likely to be machine operating hours, looking at labor, maintenance, and power cost during the period of machinery activity. Labor and materials costs are considered direct costs if they are incurred during the manufacture of a product and can be directly allocated to that product. Manufacturing overhead includes all other expenses incurred during the manufacture of a product that cannot be directly allocated to that product. This might include factory rent, payroll taxes on direct labor wages, and machine maintenance.
Traditionally, in a job order cost system and process cost system, overhead is allocated to a job or function based on direct labor hours, machine hours, or direct labor dollars. In such companies, activity‐based costing (ABC) is used to allocate overhead costs to jobs or functions. These levels include batch-level activity, unit-level activity, customer-level activity, organization-sustaining activity, and product-level activity.
It supports performance management techniques such as continuous improvement and scorecards. ABC focuses attention on cost drivers, the activities that cause costs to increase. Traditional absorption costing tends to focus on volume-related drivers, such as labour hours, while activity-based costing also uses transaction-based drivers, such as number of orders received.
In this example, the number of machine hours is the cost driver that controls how much electricity is used and the cost of maintenance. The fewer the number of machine hours, the less the cost of electricity and maintenance; whereas, the higher the number of machine hours, the more the cost of electricity and maintenance. The number of machine hours is a typical cost driver used in traditional costing systems, as is direct labor hours.
For the year, there were 2,500 labor hours worked, which in this example is the cost driver. Calculating the cost driver rate is done by dividing the $50,000 a year electric bill by the 2,500 hours, yielding a cost driver rate of $20.
Activity-based costing systems allow manufacturing companies to more accurately allocate overhead expenses to specific products, as multiple cost drivers are used. Like traditional costing systems, machine hours and direct labor hours are typical cost drivers used.
- Other examples include square footage used per product to allocate factory rent and maintenance and number of purchase orders to allocate purchasing department expenses.
- Activity-based costing systems allow manufacturing companies to more accurately allocate overhead expenses to specific products, as multiple cost drivers are used.
The other levels of activity that are accounted for by activity-based costing are unit-level activities, customer-level activities, production-level activities, and organization-sustaining activities. Direct labour and materials are relatively easy to trace directly to products, but it is more difficult to directly allocate indirect costs to products. Where products use common resources differently, some sort of weighting is needed in the cost allocation process. The cost driver is a factor that creates or drives the cost of the activity. For example, the cost of the activity of bank tellers can be ascribed to each product by measuring how long each product’s transactions (cost driver) take at the counter and then by measuring the number of each type of transaction.
ABC systems and traditional systems often result in vastly different product costs. If SailRite produces 2,000 units of the Deluxe boat, will the unit cost remain at $5,030?
Financing Business Activities
Manufacturing overhead must be accurately allocated to a product’s cost for manufacturing companies to set product sales prices and determine if products are producing profits. Activity-based costing provides a more accurate method of product/service costing, leading to more accurate pricing decisions. It increases understanding of overheads and cost drivers; and makes costly and non-value adding activities more visible, allowing managers to reduce or eliminate them. ABC enables effective challenge of operating costs to find better ways of allocating and eliminating overheads. It also enables improved product and customer profitability analysis.
Other examples include square footage used per product to allocate factory rent and maintenance and number of purchase orders to allocate purchasing department expenses. The management of Parker Company would like to use activity-based costing to allocate overhead rather than use one plantwide rate based on direct labor hours. The following estimates are for the activities and related cost drivers identified as having the greatest impact on overhead costs.
A significant portion of overhead costs are fixed and will be spread out over more units, thereby reducing the cost per unit. The point here is that managers must beware of using per unit cost information blindly for decision making, particularly if a significant change in the level of production is anticipated.
What Are Business Activities?
The number of times materials are ordered, the number of production lines in a factory, and the number of shipments made to customers are all examples of activities that impact the costs a company incurs. When using ABC, the total cost of each activity pool is divided by the total number of units of the activity to determine the cost per unit. Batch-level activities are one of the five broad levels of activity that activity-based costing account for. Each of these levels is assessed by cost, and these costs are allocated to the company’s overhead costs.
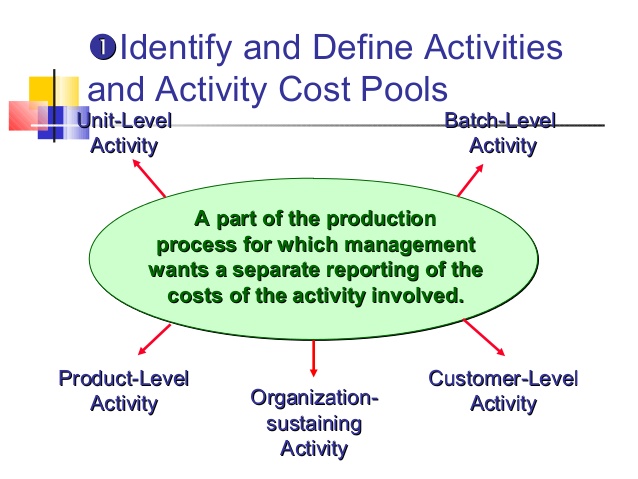
Imagine having 15 cost pools (activities), each with a predetermined overhead rate used to assign overhead costs to the company’s 80 products—not an unrealistic example for a large company. The accounting costs incurred to maintain such a system can be prohibitively high.
Organization-sustaining activities
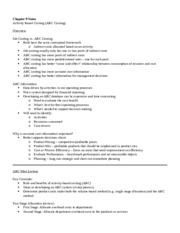
The complexity of production processes and products tended to be higher for those using ABC, and ABC companies operated at capacity more frequently. Assigning costs to activities takes time, as does identifying and tracking cost drivers. And assigning costs to products requires a significant amount of time in the accounting department.
You recognize that different products require different indirect expenses. By assigning both direct and overhead expenses to each product, you can more accurately set prices. And, the activity-based costing process shows you which overhead costs you might be able to cut back on. Second, it creates new bases for assigning overhead costs to items such that costs are allocated based on the activities that generate costs instead of on volume measures, such as machine hours or direct labor costs. For example, in a factory, the number of hours a machine runs determines how much electricity is used and how much will have to be spent on maintenance.
In this way, long-term variable overheads, traditionally considered fixed costs, can be traced to products. With activity-based costing, you take into consideration both the direct and overhead costs of creating each product.