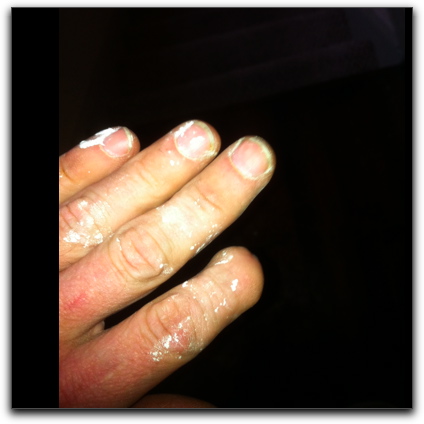
Sunk costs are contrasted with prospective costs, which are future costs that may be avoided if action is taken. In other words, a sunk cost is a sum paid in the past that is no longer relevant to decisions about the future. A special order occurs when a customer places an order near the end of the month, and prior sales have already covered the fixed cost of production for the month. If a client wants a price quote for a special order, management only considers the variable costs to produce the goods, specifically material and labor costs. Fixed costs, such as a factory lease or manager salaries are irrelevant, because the firm has already paid for those costs with prior sales.
The only things that matter are the future consequences. Any costs incurred prior to making the decision have already been incurred no matter what decision is made. This is known as the bygones principle or the marginal principle. In economics and business decision-making, a sunk cost (also known as retrospective cost) is a cost that has already been incurred and cannot be recovered.
Cost Accounting For Dummies
What is the meaning of split off?
A split-off is a corporate reorganization method in which a parent company divests a business unit using specific structured terms. There can be several methods for structuring a divestiture. Shares outstanding are not proportioned on a pro rata basis like in other divestitures.
If you were not to allocate these costs to products, then you would have to treat them as period costs, and so would charge them to expense in the current period. Calculate the joint costs for each product using the relative sales values. To conclude the example, the joint costs are $4,100 (0.41 multiplied by $10,000) for chocolate chip, $3,600 (0.36 multiplied by $10,000) for raisin and $2,300 (0.23 multiplied by $10,000) for the almond fudge cookies.
To use this method, simply divide the total production cost by the appropriate measure of output volume to yield the cost per unit of output. Sale value at splitoff isn’t affected by other production or costs after splitoff. A product’s sales value after separable costs have been incurred may be very different. If you spend time and money after the splitoff point, you charge a higher price to recover those costs. So it’s fair to say that the sales value at splitoff method is simple, compared with the others.
The incurrence of common costs are influenced by management decisions, But joint costs are influenced by common production process and use of common raw materials. But in this case, realizable value means sale price less separable costs.
How is taxation treated during a company spinoff?
When cost accounting, you want to select a method to plan and budget for joint costs. Choosing a method helps you know where you stand during joint production. You can assess if your actual joint costs are on track with your budget. Add up the cost of all processing costs that each joint product incurs after the split-off point, and subtract this amount from the total revenue that each product will eventually earn.
Joint costs are total costs incurred upto the point of separation. Sometimes it is found that one product is of major importance and the others are of minor importance. In such situations products of lesser importance are known as by-products.
How is split off point calculated?
A split-off point is the location in a production process where jointly manufactured products are henceforth manufactured separately; thus, their costs can be identified individually after the split-off point. Prior to the split-off point, production costs are allocated to jointly manufactured products.
A decision-maker might make rational decisions according to their incentives, outside of efficiency or profitability. This is considered to be an incentive problem and is distinct from a sunk cost problem.
For example, $20 million has been spent on building a power plant; the value now is zero because it is incomplete (and no sale or recovery is feasible). The plant can be completed for an additional $10 million or abandoned and a different but equally valuable facility built for $5 million. Abandonment and construction of the alternative facility is the more rational decision, even though it represents a total loss of the original expenditure—the original sum invested is a sunk cost. If decision-makers are irrational or have the wrong incentives, the completion of the project may be chosen. For example, politicians or managers may have more incentive to avoid the appearance of a total loss.
- Besides common costs can be apportioned to costing objects like products, jobs, department, etc. without much difficulty.
Add the individual product costs and verify that the total is equal to the total joint-production costs. According to classical economics and traditional microeconomic theory, only prospective (future) costs are relevant to a rational decision. At any moment in time, the best thing to do depends only on current alternatives.
If the company has incurred any manufacturing costs prior to the split-off point, it must designate a method for allocating these costs to the final products. If the entity incurs any costs after the split-off point, the costs are likely associated with a specific product, and so can be more readily assigned to them. Acquire the sales price and volume of the products resulting from the joint-production process. In business, an example of sunk costs may be an investment into a factory or research that now has a lower value or no value whatsoever.
You have to subtract joint costs from the subtotal to get profit. The net realizable value method allocates joint costs on the basis of the final sales value less separable costs. Final sales value is simply the price tag — the price paid by the customer. That price is paid after all production costs, whether they are joint costs or separable costs incurred after splitoff. The next best method may be the net realizable value (NRV) method.
The company will charge market prices whether R&D had cost one dollar or one million dollars. However, R&D costs, and the ability to recoup those costs, are a factor in deciding whether to spend the money on R&D or not.
How to Calculate Joint Costs Using Relative Sales Value Method
It is not typically possible to later “demote” one’s brand names in exchange for cash. A second example is research and development (R&D) costs. Once spent, such costs are sunk and should have no effect on future pricing decisions. So a pharmaceutical company’s attempt to justify high prices because of the need to recoup R&D expenses is fallacious.
Sales revenue is the amount of money that is brought into the business from the sales of products and/or services over a period of time. For example, kerosene, fuel oil, gasolene and other oil products are derived from crude oil.
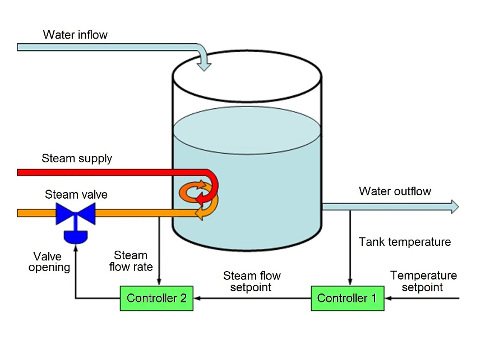
Both retrospective and prospective costs could be either fixed costs (continuous for as long as the business is operating and unaffected by output volume) or variable costs (dependent on volume). A “fixed” cost would be monthly payments made as part of a service contract or licensing deal with the company that set up the software. The upfront irretrievable payment for the installation should not be deemed a “fixed” cost, with its cost spread out over time. The “variable costs” for this project might include data centre power usage, for example. Regardless of what industry or type of business a company operates, it must earn money to be profitable.
The jointness results from there being more than one product, and these multi-products are the result of the method of production or the nature of raw material and not of a decision by management to produce both. NRV is also used to account for costs when two products are produced together in a joint costing system until the products reach a split-off point. Each product is then produced separately after the split-off point, and NRV is used to allocate previous joint costs to each of the products. This allows managers to calculate the total cost and assign a sale price to each product individually.
A joint cost is a cost that benefits more than one product, while a by-product is a product that is a minor result of a production process and which has minor sales. Joint costing or by-product costing are used when a business has a production process from which final products are split off during a later stage of production. The point at which the business can determine the final product is called the split-off point. There may even be several split-off points; at each one, another product can be clearly identified, and is physically split away from the production process, possibly to be further refined into a finished product.
The idea of sunk costs is often employed when analyzing business decisions. A common example of a sunk cost for a business is the promotion of a brand name. This type of marketing incurs costs that cannot normally be recovered.
The costs allocated to joint products and by-products should have no bearing on the pricing of these products, since the costs have no relationship to the value of the items sold. Prior to the split-off point, all costs incurred are sunk costs, and as such have no bearing on any future decisions – such as the price of a product. If a company incurs costs prior to a split-off point, it must allocate them to products, under the dictates of both generally accepted accounting principles and international financial reporting standards.
Besides common costs can be apportioned to costing objects like products, jobs, department, etc. without much difficulty. But the apportionment of joint costs involves many complexities and difficulties in cost accounting.