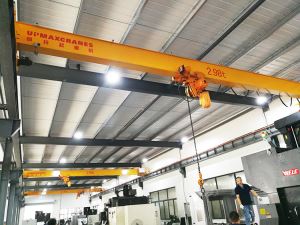
In construction, all costs which are required for completion of the installation, but are not directly attributable to the cost object are indirect, such as overhead. In manufacturing, costs not directly assignable to the end product or process are indirect. These may be costs for management, insurance, taxes, or maintenance, for example. Indirect costs are those for activities or services that benefit more than one project.
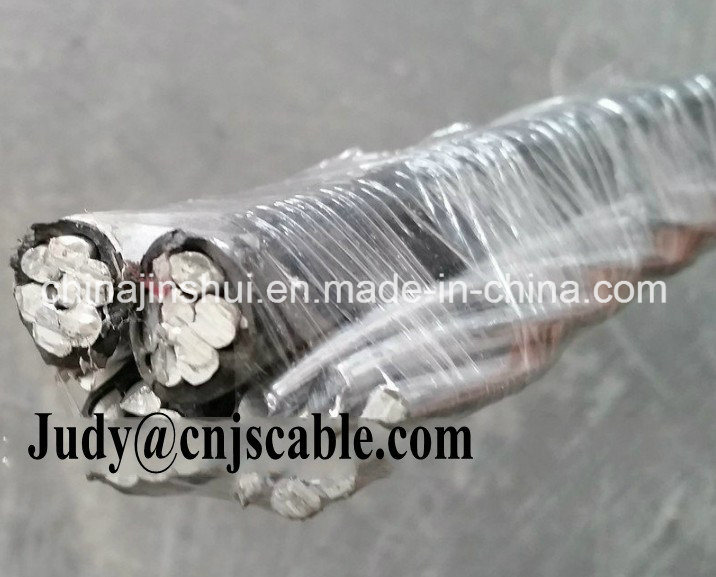
Fixed expenses are those that must be paid each month. These can include rent or mortgage payments, depreciation of assets, salaries and payroll, membership and subscription dues, legal fees and accounting costs.
Overhead does not include non-factory business expenses like selling, general and administrative expenses. Suppose you find the sum of these and other overhead costs for the ABC Company are likely to be $1.4 million. This is the projected manufacturing overhead for the next year. To calculate manufacturing overhead, you need to add all the indirect factory-related expenses incurred in manufacturing a product. This includes the costs of indirect materials, indirect labor, machine repairs, depreciation, factory supplies, insurance, electricity and more.
Fixed expense amounts stay the same regardless if a business earns more — or loses more — in revenue that month. Associated payroll costs, including outsourcing payroll services, are included in the fixed expense category. Labor costs, such as employee time, that are not chargeable to a direct manufacturing or production activity also fall under fixed expenses.
Impact on Overhead Allocation on Balance Sheet
These accountants are adding direct materials, direct labor and applied overhead to jobs to calculate the cost of goods sold on every job that is sold. The second group of accountants is recording actual bills and totalling up actual overhead costs. Except these actual overhead costs are not included in cost of goods sold. The allocation base is the basis on which a business assigns overhead costs to products. The commonly used allocation bases in manufacturing are direct machine hours and direct labor hours.
Selling, general, and administrative expenses are all classified as non-manufacturing. For instance, if your client owns Bubbles Bubblegum Company, the cost of ingredients, labour to make the gum, and the machinery that makes the gum are manufacturing overhead costs.
To calculate the overhead costs of a business, add all the ongoing business expenses that keep your business running but do not contribute to the revenue generation process. These are indirect costs such as administrative expenses, selling and marketing costs and production expenses.
For example, a firm finds that the overhead cost payments for one month total $15,000. The overhead application rate, also called the predetermined overhead rate, is often used in cost and managerial accounting for calculating variances. The basic formula to calculate the overhead application rate is to divide the budgeted overhead at a particular rate of output by the budgeted activity for the rate of output. Non-manufacturing overhead costs are expenses that your client’s company must pay but aren’t directly related to making the product.
Since the total amount of machine-hours used in the accounting period was 7,200 hours, the company would apply $257,400 of overhead to the units produced in that period. From a management perspective, the analysis of applied overhead (and underapplied overhead) is a standard part of financial planning & analysis (FP&A) methods. By carefully reviewing how costs are assigned to certain products or projects, management teams can make better-informed capital budgeting decisions. In turn, with better results, management can drive the cost of capital lower, thereby increasing business valuation.
Make a comprehensive list of indirect business expenses including items like rent, taxes, utilities, office equipment, factory maintenance etc. Direct expenses related to the production of goods and services, such as labor and raw materials, are not included in overhead costs. For instance, a business may apply overhead to its products based on standard overhead application rate of $35.75 per hour of machine & equipment time used.
- Manufacturing overhead is a term used to describe the indirect costs associated with making a product.
Non-Manufacturing Overhead
In business, overhead or overhead expense refers to an ongoing expense of operating a business. Overheads are the expenditure which cannot be conveniently traced to or identified with any particular cost unit, unlike operating expenses such as raw material and labor. Therefore, overheads cannot be immediately associated with the products or services being offered, thus do not directly generate profits. However, overheads are still vital to business operations as they provide critical support for the business to carry out profit making activities.
Accuracy when it comes to allocating overhead costs per unit of production is important for pricing purposes. When you add direct labor and direct materials costs to the overhead allocation, the result provides a reliable estimate of the cost of manufacturing. When a factory operation is labor-intensive, basing overhead allocation on direct labor hours provides an accurate estimate because the overhead cost will correlate closely with the labor used. However, it is important to use up-to-date figures when determining manufacturing overhead since these expenses will change over time.
Manufacturing overhead is a term used to describe the indirect costs associated with making a product. Overhead costs are expenses required for the manufacturing process other than the direct costs of labor and materials. Businesses engaged in manufacturing usually allocate manufacturing overhead costs as a proportion of some amount linked to the production process for accounting, cost control and pricing purposes. For some firms, calculating overhead costs based on direct labor hours works well.
The overhead is attributed to a product or service on the basis of direct labor hours, machine hours, direct labor cost etc. The overhead absorption rate is calculated to include the overhead in the cost of production of goods and services.
For example, overhead costs such as the rent for a factory allows workers to manufacture products which can then be sold for a profit. Overheads are also very important cost element along with direct materials and direct labor. Overhead includes electricity, insurance, factory supplies other than direct materials and depreciation. It also includes the cost of shop floor managers, inspectors and maintenance workers.
While some of these costs are fixed such as the rent of the factory, others may vary with an increase or decrease in production. To calculate the manufacturing overhead, identify the manufacturing overhead costs that help production run as smoothly as possible. Add all the indirect costs to calculate the manufacturing overhead. Indirect costs are, but not necessarily, not directly attributable to a cost object. Indirect costs are typically allocated to a cost object on some basis.
Selecting Cost Drivers
Total cost of a product involves direct costs and indirect costs. Direct costs can be conveniently traced down to the product manufactured. It includes direct materials, direct wages, and direct expenses. On the other hand, indirect costs cannot be identified with the product manufactured.
Examples of direct costs are direct labor, direct materials, commissions, piece rate wages, and manufacturing supplies. Examples of indirect costs are production supervision salaries, quality control costs, insurance, and depreciation. Overhead costs include rent, indirect materials, labor and any other costs not directly associated with production.
Overhead application
It’s used to define the amount to be debited for indirect labor, material and other indirect expenses for production to the work in progress. So far, we haven’t used a singleactual overhead figure in our calculations. Actual overhead is the amount that the company actually incurred. Imagine that there are two groups of accountants inside a company. One group is applying overhead based on the actual activity and the predetermined overhead rate.
Why is overhead application important?
Overhead application is the assignment of factory overhead costs to the units produced in a reporting period. The assignment is based on either a standard overhead rate that is used for multiple time periods, or a calculation that is specific to each reporting period.