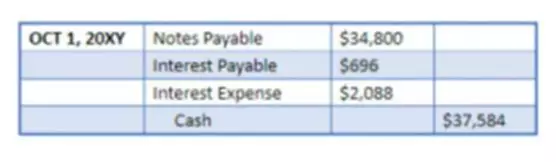
For example, a manufacturer of made-to-order furniture would likely employ job costing. The last-in-first-out (LIFO) inventory valuation method is the opposite of the FIFO approach. Getting expert tax and accounting advice is worthwhile for virtually every business. A Certified Public Accountant (CPA) with experience in your industry can provide valuable financial insight and ensure you meet your tax obligations. Manufacturing overheads might include the costs for powering a factory’s equipment and personnel not directly involved in producing the product. To reduce the costs of doing business, you must understand first where your production costs lie.
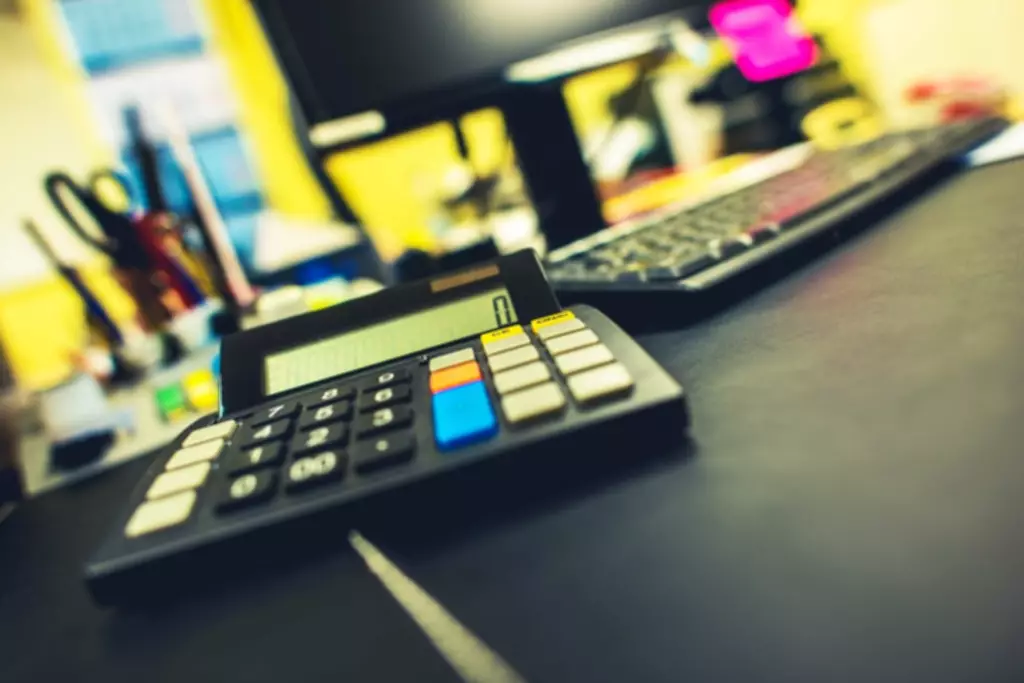
The job order costing method calculates costs per manufacturing project or unit, making it useful for make-to-order manufacturers, construction manufacturers, and the like. It is based on calculating standard rates for the direct and indirect costs of products. These predetermined “standards” are usually based on the company’s previous experiences and are routinely updated to reflect market fluctuations. Having a manufacturing account includes increased efficiency, better cash flow management, informed decision-making, and improved financial planning. Finished goods inventory refers to the units that have made it through the production process and are ready for sale.
5.4 Level of Detail
He now writes articles on personal and corporate finance, accounting and tax matters, and entrepreneurship. Manufacturers of highly differentiated products need to track costs for each unit so they can set prices appropriately and monitor the profitability of their products. This approach is primarily beneficial for manufacturers who produce a relatively low number of unique products.
Depending on your business model, you may prefer to structure your accounting around individual units, product lines, or processes. Your manufacturing accounting software should also help you keep compliant with regulations and the tax laws of the countries you have a business in. Often, manufacturers invest in an all-in-one solution, which handles other tasks away from finances, such as planning and production. Ideally, data should move freely between production lines and the back office, meaning you have accurate real-time data. If job costing is ideal for manufacturing businesses that produce lower numbers of unique products, process costing is for those that create a high volume of homogenous units.
Best practices in manufacturing accounting
All such information is provided solely for convenience purposes only and all users thereof should be guided accordingly. The finished goods Manufacturing account represents all finished products ready for sale. Apply for financing, track your business cashflow, and more with a single lendio account. Inventory is continually being sold and restocked, so you may need to make a cost flow assumption. Lean manufacturing is all about minimizing waste while maximizing productivity. It is a practice first initiated by Toyota but has influenced manufacturing for decades, particularly the automobile industry.
- Some of the benefits of having a Manufacturing account include increased efficiency, improved cash flow, better budgeting, greater flexibility, and the ability to save time and money.
- Working closely with manufacturers on case studies and peering deeply into a plethora of manufacturing topics, Mattias always makes sure his writing is insightful and well-informed.
- When you can estimate how much it’ll cost to produce each unit, you can gauge your progress during each accounting period.
- These standards guide accountants when preparing financial statements to ensure that all financial reports are consistent with accepted practices in the field.
- This is better for high-value items that need differentiation, rather than interchangeable items.
- In addition, there are three subledger types (X, Y, and Z) that you can define with user defined codes (system 00, type ST).
Our mission is to empower readers with the most factual and reliable financial information possible to help them make informed decisions for their individual needs. This includes wages paid for workers who operate machines, assemble products or package goods. Because you must get special permission from the IRS to change your accounting basis later, it’s best to get it right the first time. These articles and related content is the property of The Sage Group plc or its contractors or its licensors (“Sage”). Please do not copy, reproduce, modify, distribute or disburse without express consent from Sage.
It is a tool that companies can use to help manage the finances and inventory of a manufacturing company. Variable costs change depending on the number of units your manufacturing firm produces. A direct cost is an expense that you can easily trace to product manufacturing processes. ABC systems involve sorting your business’s indirect costs into groups, calculating a per-unit rate based on their primary cost drivers, then using that rate to allocate costs to products or activities. Activity-based costing (ABC) is a way to assign indirect manufacturing costs like overhead to products or processes.
Overview to Manufacturing Accounting
ABC is a very accurate costing methodology that helps to factor indirect costs into unit pricing. It can be more difficult to implement than standard or job costing, however, as a more detailed overview is required over the manufacturing process. This costing method is similar to job costing, however, it calculates item costs by adding together the direct costs and overheads per processing step of a product’s lifecycle, rather than per individual item or job. This makes it a favorable costing method for process manufacturers and other companies that otherwise produce large numbers of identical units. From inventory management to payroll and accounts payable, accounting software helps manage the financial aspects of a business. Inventory valuation, direct labor and manufacturing overhead costs are just part of the recipe that is cost accounting in the manufacturing industry.
The International Financial Reporting Standards (IFRS) prohibits it, and businesses in the United States may not be able to use it forever. Manufacturing accounting follows the same fundamental principles as accounting in other industries, but there are many more moving parts than usual. Let’s look at some general best practices you should follow to optimize your accounting system.
While these types of accounting are certainly important, they don’t provide the same level of detail and insight into manufacturing operations as manufacturing accounting does. Manufacturing accounting is a specialized form of accounting that focuses on the needs of the manufacturing industry. It is designed to provide a comprehensive and detailed view of the financial performance of a manufacturing business.
Most manufacturers use bills of materials (BOMs) to track the components needed for each product. Keeping accurate financial records is vital for any business, but manufacturing is even more essential. Manufacturing accounting is a specialized field that requires a deeper understanding of the industry and its unique processes and costs. Your manufacturing business is as creative and unique as you are, so it goes without saying your accounting software should be too. Manufacturers will often seek out a modularized all-in-one solution, where every facet of the business,s such as inventory, tracking, production, and planning, are combined into one system. These types of highly extensible systems are known as Enterprise Resource Planning (ERP) platforms.
This will result in you having better insights into what everything costs to manufacture and how much you should charge for the items you’re making. This will help to identify opportunities to improve efficiencies companywide, drive revenue and increase profit. Inventory management is also a crucial component of manufacturing accounting. By carefully managing your inventory levels, you can ensure that you have enough raw materials and finished goods to meet demand without tying up too much cash in excess inventory. A manufacturing account tracks a manufacturing business’s production costs, materials used, and inventory levels. This account can track production costs, materials used, and inventory levels.
Get manufacturing know-how delivered to your inbox!
Direct labor costs typically include wages paid for regular hours, overtime and payroll tax information. The chart of accounts is a record of the valid accounts you assign to the business units within your company’s reporting structure. When you set up your chart of accounts, you define the location of the accounts using automatic accounting instructions (AAIs) that indicate which number ranges represent assets, liabilities, and so on. The system underlines LOD 3 on balance sheet reports and LODs 3 and 4 on income statement reports. This information helps companies arrive at better decisions about when to buy materials and sell products. Moreover, it is dubbed a complete business because it buys the raw materials used to create a product before selling it.
A Manufacturing account tracks a manufacturing business’s production costs, materials used, and inventory levels. A Factory Overhead account tracks the expenses that a manufacturing business incurs to operate its factory. Features found in accounting software such as inventory management can help you optimize the way you use inventory, such as providing alerts when your stock needs replenishing.
Manufacturing accounting: a unique approach for a unique sector
Since then, many other industries have come to regard removing waste from their processes as beneficial to the bottom line. This insight is invaluable for businesses looking to maximize their profit margins while still providing a high-quality product or service for their customers. In recent years, technology has changed the way accountants work with faster access to data while also making it easier for them to analyze large amounts of information quickly and accurately.
These would include expenses such as storage facility or warehouse mortgage fees, bank loans, machinery and equipment depreciation, and some labor costs. Insight into variable and fixed costs helps manufacturers make decisions on production volumes, adjust to market trends, etc. To understand why manufacturing accounting differs from other accounting forms, one must first understand how manufacturers produce their products.
Because manufacturers carry significant inventories, they need to know how to track their costs to create accurate financial statements and comply with accounting standards. The overhead cost of a cost pool is then divided by the number of units in the activity to arrive at the activity rate – a fixed amount that is added to each unit’s cost. For a manufacturing company that uses the periodic inventory method, closing entries update retained earnings for net income or loss and adjust each inventory account to its period end balance. A special account called manufacturing summary is used to close all the accounts whose amounts are used to calculate cost of goods manufactured. The closing entries that follow are based on the accounts included in the cost of goods manufactured schedule and income statement for Red Car, Inc. A Manufacturing account is an internal financial statement that businesses use to track their production costs, materials used, and inventory levels.