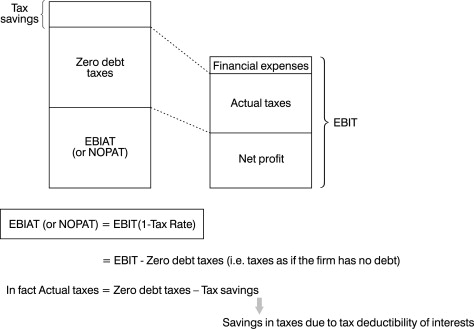
Examples of Uses for Net Realizable Value
So it’s fair to say that the sales value at splitoff method is simple, compared with the others. Acquire the sales price and volume of the products resulting from the joint-production process. One type of monetary measure of joint cost allocation is the sales value method. Using the sales value method, separate and differentiate the primary products according to sales value. Then divide them into proportions of sales value that add up to 100%.
Sale value at splitoff isn’t affected by other production or costs after splitoff. A product’s sales value after separable costs have been incurred may be very different. If you spend time and money after the splitoff point, you charge a higher price to recover those costs.
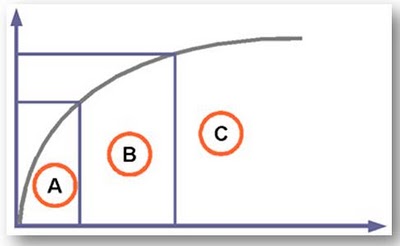
If the entity incurs any costs after the split-off point, the costs are likely associated with a specific product, and so can be more readily assigned to them. Calculate the joint costs for each product using the relative sales values.
For starters, your production process after splitoff may change. Hopefully, you’re able to review variance results and improve the process. If you change your production after splitoff, your separable cost totals change. But in this case, realizable value means sale price less separable costs. You have to subtract joint costs from the subtotal to get profit.
All companies make their products and services unique and offer them at different price levels. Their aim is to capture the specific customers that will enable the company to maximize profit. Large market share, whether measured in units sold or total revenues, does not always correlate with high profitability. For example, the market share of General Motors in 2011 was 19.4%, more than 6 times the share of BMW at 2.82%. GM reported profits of $9.2 billion while BMW reported profits of about $4.9 billion Euros ($5.3 billion U.S.) during the same period.
Besides common costs can be apportioned to costing objects like products, jobs, department, etc. without much difficulty. But the apportionment of joint costs involves many complexities and difficulties in cost accounting. The incurrence of common costs are influenced by management decisions, But joint costs are influenced by common production process and use of common raw materials.
If your total costs come in lower than expected, maybe you can price the product lower than $50, and that might increase sales. Which of the methods of allocating joint costs usually is considered the simplest to implement?
This allows managers to calculate the total cost and assign a sale price to each product individually. The NRV method also does a good job of matching the benefit received (final sales value) with the costs incurred (separable costs).
Let’s say out of it, Walmart is going to sell some part of the inventory to another company for $4 Bn for offloading purposes. For that Walmart needs to calculate the cost associated with the Sale of Inventory. Let’s say transportation cost is $500 Mn and legal and registration charges are $100 Mn. In the table, the cost per unit is the same for both products. That’s because the joint cost allocation isn’t related to cost because it uses the physical measure method.
NRV is also used to account for costs when two products are produced together in a joint costing system until the products reach a split-off point. Each product is then produced separately after the split-off point, and NRV is used to allocate previous joint costs to each of the products.
A) estimated net realizable value B) constant gross-margin percentage NRV C) sales value at splitoff D) All of these answers are correct. A joint cost is a cost that benefits more than one product, while a by-product is a product that is a minor result of a production process and which has minor sales. Joint costing or by-product costing are used when a business has a production process from which final products are split off during a later stage of production. The point at which the business can determine the final product is called the split-off point. If the company has incurred any manufacturing costs prior to the split-off point, it must designate a method for allocating these costs to the final products.
By-product costing and joint product costing
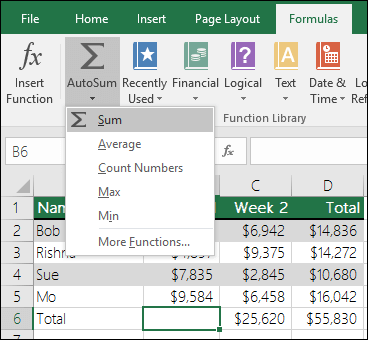
You also see the physical measures method of allocating joint costs. The Percent of NRV total is the percentage of the total NRV for each product. The $760,000 of NRV for Sassy purses is 55.88 percent of the total of $1,360,000. Then you multiply $900,000 in total joint costs by the percentage, and that allocates joint costs to each purse.
- The next best method may be the net realizable value (NRV) method.
- The net realizable value method allocates joint costs on the basis of the final sales value less separable costs.
Your crews cut down trees and produces two types of lumber for the construction industry. Both types are two-by-fours (two inches by four inches by eight feet in length). Winter Pine is the more expensive product; the all-year-use two-by-fours are cheaper.
How to Calculate Joint Costs Using Relative Sales Value Method
Which joint cost allocation method is best?
The splitoff method in cost accounting After splitoff, each product incurs separable (or independent) costs. Allocating joint costs using sales value at splitoff may be the most effective method for planning and budgeting for joint costs.
The next best method may be the net realizable value (NRV) method. The net realizable value method allocates joint costs on the basis of the final sales value less separable costs. Final sales value is simply the price tag — the price paid by the customer. That price is paid after all production costs, whether they are joint costs or separable costs incurred after splitoff.
The following table explains how to allocate $208,000 in joint costs using the relative sales value method. One issue with the net realizable value (NRV) method is that amounts may change.
Practice: Sales Value at Split-off
Whether measured by per unit sales or total revenue, BMW showed a higher degree of profitability than GM. Profit per unit, not just market share, is the goal of most companies.
NPV captures any changes to costs and sale price that might occur as products are produced separately. You can allocate joint costs based on the revenue the units generate. Market refers to the market value (sales value) of the product. The market-based method you see here is the sales value at splitoff method.
Because you’re allocating based on number of units, the cost attached to all units is the same. You’re not weighting the cost allocation based on sales value. The physical measure method allocates cost by the weight, volume, or some other measurement of the product that’s produced. In this case, assume that the weight or volume for each two-by-four is the same. (Well, yeah. They are both two-by-fours.) So you allocate joint costs based on the number of units produced.
What Is Net Realizable Value?
The latter are easily identified and traced to the individual products, and no problem of apportionment is involved in such costs. Walmart is a US-based retail supermarket chain-based company with around $500Bn of revenue as per the financial year 2018. Let’s say in the Financial year 2018, a market value of Inventory (which is also an asset) for Walmart is around $44 Bn.
Joint costs can be apportioned to different products only by means of some suitable bases of apportionment. Total costs of production of multiple products combine both joint costs and separable individual product costs.
Add the individual product costs and verify that the total is equal to the total joint-production costs. However, it is not feasible to have separate assembly lines for each product, which means that there might be one or more steps in the process where there is joint production.
Then multiply the percentage proportions by the total production cost to yield the allocated cost per primary product type. To use this method, simply divide the total production cost by the appropriate measure of output volume to yield the cost per unit of output. You may not be able to price your product until after production ends. And in a market with heavy competition, to maintain your sales levels, you have to keep your price competitive (for the Sassy purses, say $50 per unit or lower).
How do you calculate allocated joint cost?
The relative-sales-value method allocates costs based on the relative sales value of each resulting from a joint-production process. Divide the sales value of each product by the total sales to determine the relative sales value of each product.
Making a calculation after production ends has some other benefits. The NRV method accounts for all separable costs, regardless of how much higher or lower they are than your plan. NRV also handles any change to the final sales value (price tag) due to a change in market conditions.
The split-off point is the point at which joint production stops and processing for separate products begins. The relative-sales-value method allocates costs based on the relative sales value of each resulting from a joint-production process.