A Complete Guide for Small Businesses
If any remainder materials are later returned to the warehouse, their cost is then subtracted from the job and they are returned to storage. A job costing system involves the process of accumulating information about the costs associated with a specific production or service job. This information may be required in order to submit the cost information to a customer under a contract where costs are reimbursed. The information is also useful for determining the accuracy of a company’s estimating system, which should be able to quote prices that allow for a reasonable profit.
It can help to get an estimate from each of these contractors. Job costing involves the detailed accumulation of production costs attributable to specific units or groups of units. For example, the construction of a custom-designed piece of furniture would be accounted for with a job costing system. The costs of all labor worked on that specific item of furniture would be recorded on a time sheet and then compiled on a cost sheet for that job. Similarly, any wood or other parts used in the construction of the furniture would be charged to the production job linked to that piece of furniture.
Differences Process Costing Job Costing Unit cost information comes from the departmental production cost report. Inventory Accounts Similarities Inventory accounts include raw materials inventory, work-in-process inventory, and finished goods inventory. Differences Process Costing Job Costing Several different work-in-process inventory accounts are used—one for each department (or process). One work-in-process inventory account is used—job cost sheets track costs assigned to each job. Recall the three components of product costs—direct materials, direct labor, and manufacturing overhead.
How is job cost calculated?
A job cost record forms part of a job cost system, and is used to accumulate manufacturing costs of direct materials, direct labor, and applied overhead for a particular job.
The information can also be used to assign inventoriable costs to manufactured goods. A price for the job is to be conveyed to the customer while accepting a job. The proposed materials are taken into account and their accurate market value is considered. Overhead absorption rate is followed for estimating factory overhead.
Job Cost Record Template
Differences Process Costing Job Costing Product costs are assigned to departments (or processes). Unit Cost Information Similarities Unit cost information is needed by management for decision-making purposes.
Each job is pass on various departments according to the nature of job to be completed but not through all the departments. Job costing is otherwise called as job order costing, job cost accounting, specific order costing, production order costing, job lot costing and lot costing. Job means a piece of work done by the worker in an organization.
Calculate Labor Costs
Multiply the payroll day rate by the amount of time you estimate you’ll need to complete the job. If you’ll rely on subcontractors for work your company doesn’t complete itself, factor those costs into your total labor costs for the job.
- Now that you’ve calculated your predetermined overhead rate, you can apply it to jobs for the purpose of job costing, as the applied overhead cost.
- Job costing is an accounting tool that allows businesses to track costs by individual jobs.
Who Uses Job Costing?
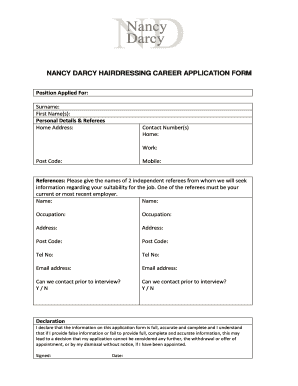
You also estimate that your employees will work 10,000 hours in 2020. Job costing, also called project-based accounting, is the process of tracking costs and revenue for each individual project. Job costing looks at each project in detail, breaking down the costs of labor, materials and overhead. It makes fewer assumptions than other costing methods. The job costing system must be able to track the cost of materials that are used or scrapped during the course of the job.
Thus, if a business is constructing a custom-made machine, the cost of the sheet metal used in the construction must be accumulated and charged to the job. The system can compile this cost through the manual tracking of materials on costing sheets, or the information can be charged by using on-line terminals in the warehouse and production area. Typically, materials are kitted for a job in the warehouse, and are charged to a specific job at that time.
You’ll need to estimate the total overhead costs factoring into the job, including rent on your office, administrative costs and depreciation on the equipment used. Many businesses apply a blanket overhead fee to each project, such as 10 percent per job. An accountant can help you analyze your business and develop a specific approach to overhead. Or, you can calculate your predetermined overhead rate. Calculate how much it costs your business to employ all staff members who will work on the project per day.
Job Costing Example
Job costing is an accounting tool that allows businesses to track costs by individual jobs. Job costing is calculated by accumulating the cost of labor, materials and overhead for a specific project.
The job costing system assigns overhead costs (such as depreciation on production equipment and building rent) to one or more cost pools. At the end of each accounting period, the total amount in each cost pool is assigned to the various open jobs based on some allocation methodology that is consistently applied. The main purpose of job costing is to determine the profit or loss on each job. The estimated costs are recorded in the job cost sheet and the actual incurred costs are also collected for each job separately.
Assigning these product costs to individual products remains an important goal for process costing, just as with job costing. However, instead of assigning product costs to individual jobs (shown on a job cost sheet), process costing assigns these costs to departments (shown on a departmental production cost report). Overhead is the most difficult cost to calculate, because you’ll need to rely on an approximation instead of a more exact figure.
How do you do a job order cost sheet?
Job costing involves the accumulation of the costs of materials, labor, and overhead for a specific job. For example, job costing is appropriate for deriving the cost of constructing a custom machine, designing a software program, constructing a building, or manufacturing a small batch of products.
The time required to complete a job is shorter than the time required to complete a contract. But, the principles followed in job costing and contract costing is one and the same. Jobs are normally carried out in workshops while contracts are mostly executed in outside. In a factory, jobs are carried out in different departments.
Now that you’ve calculated your predetermined overhead rate, you can apply it to jobs for the purpose of job costing, as the applied overhead cost. For each direct labor hour worked, you’ll add $5 of overhead to the job. Job costing, generally, means a specific accounting methodology used to track the expense of creating a unique product. Job costing forms have spaces to include direct labor, direct materials, and overhead. Product Costs Similarities Product costs consist of direct materials, direct labor, and manufacturing overhead.
Then, a comparison of actual cost is made with the estimated cost in respect of each job to know the level of profit. You want to use job costing in your construction business, and you’re looking to calculate your predetermined overhead rate to use for job costing. You estimate that in 2020, you’ll have $500,000.00 in overhead costs.