What Is Production Volume Variance?
Production volume variance is a statistic used by businesses to measure the cost of production of goods against the expectations reflected in the budget. It compares the actual overhead costs per unit that were achieved to the expected or budgeted cost per item. To calculate overhead efficiency variance, subtract the budgeted labor hours from the actual hours expended and multiply by the standard overhead rate per hour. For example, say a company budgeted for 20 labor hours but only used 16 and the standard overhead rate is $5 per hour.
How do you calculate production volume?
Production volume measures the total amount your company can produce over time. This KPI tracks the total number of products manufactured over a set period of time (days, weeks, months, quarters, years) and focuses on total output.
Two costing methodologies, actual costing and normal costing, assist businesses in evaluating production costs. Actual costing uses the actual cost of materials and labor to calculate production costs.
For this reason, some businesses prefer to rely on other statistics, such as the number of units that can be produced per day at a set cost. Sales volume equals the quantity of items a business sells during a given period, such as a year or fiscal quarter. Sales — or sales revenue — equals the dollar amount a company makes during the period under review. The concepts of sales and sales volume interconnect because total sales equal sales volume multiplied by the unit price. For example, a company sold 1 million units of a product at $2 apiece.
As a result, the corporate sales volume is 1 million, yielding periodic sales of $2 million, or 1 million multiplied by $2. It is a general rule that in the calculation of actual overhead rate, actual overheads will be divided with the actual quantity and not with the budgeted quantity. The reason for this rule is simple as this provides more authentic results as you are comparing the like terms.
Using the first actual costing formula, these numbers make up the labor portion of the production costs. Direct labor volume variance – also called direct labor efficiency variance — is the difference between the amount of direct labor hours budgeted and the actual hours expended. Direct labor hours are the hours spent by the individuals that actually create or modify the product. To calculate direct labor efficiency variance, subtract the budgeted labor hours from the actual hours expended and multiply by the budgeted cost of labor per hour. For example, if a company thought it would need 20 labor hours at $30 per hour for a product but only needed 16 hours, the variance is 4 multiplied by $30, or $120.
How are fixed and variable overhead different?
After all the calculations are done, add up the totals and you’ll get the actual cost of producing your product. In other words, managers go back to the source of the costs (cost objects) like labor and materials. Managers can analyze how many hours of manufacturing time a product requires to calculate the actual costs of producing that product. Normal costing is a method of costing that is used in the derivation of cost.
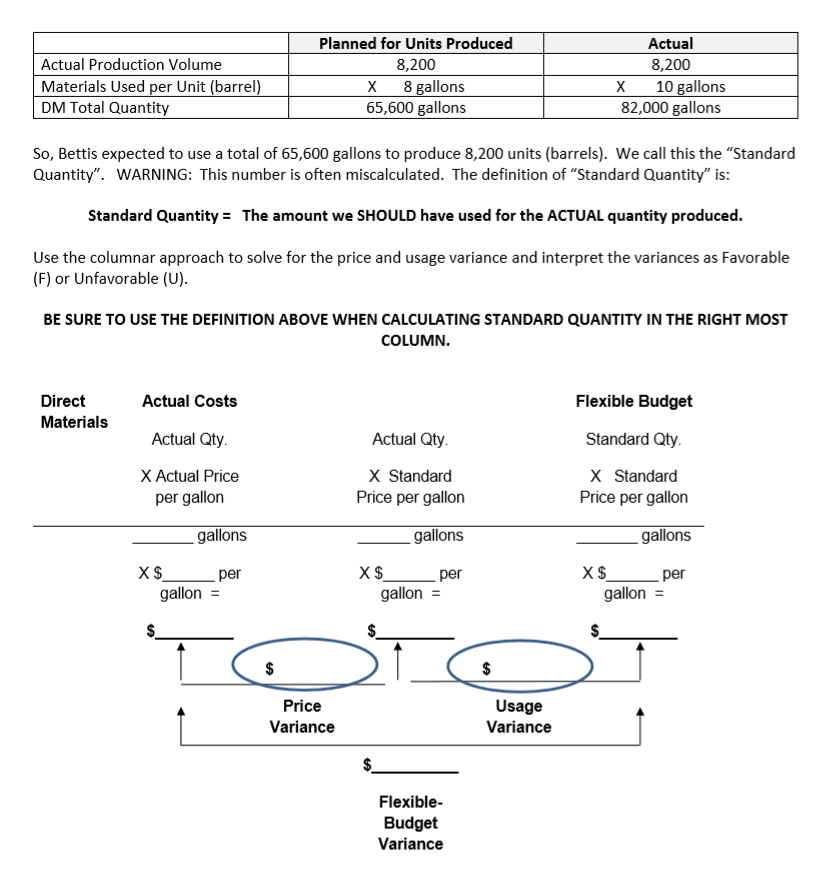
Volume variance can be applied to units of sales, direct materials, direct labor hours and manufacturing overhead. The basic formula for volume variance is the budgeted amount less the actual amount used multiplied by the budgeted price.
- A business measures its manufacturing and selling efficiency by examining any volume variances it incurs during production and sales.
- A volume variance is the difference between what a company expected to use and what it actually used.
- Volume variance can be applied to units of sales, direct materials, direct labor hours and manufacturing overhead.
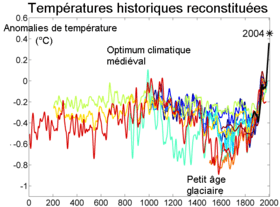
How is absorption costing treated under GAAP?
For example, if a company expected to sell 20 widgets at $100 a piece but only sold 15, the variance is 5 multiplied by $100, or $500. To calculate direct materials quantity variance, subtract the budgeted direct materials needed from the actual quantity used and multiply by the budgeted cost of direct materials. For example, if a company thought it would need 7 yards of fabric at $6 a yard for a product but only needed 5 yards, the variance is 2 multiplied by $6, or $12. It may be calculated against a budget that was drafted months or even years before actual production.
Production volume variance is favorable if actual production is greater than budgeted production. Since overhead like utility usage is a little difficult to assign to a single product, managers usually make estimates. They estimate how much overhead was used and how long the overhead was used. Using the second actual costing formula, management can determine the indirect productions costs for producing the product.
A favorable overhead variance, like this one, means that less overhead costs were spent to create the product than expected. If the variance is negative, that means that more hours were spent on the product than expected, and more overhead costs were incurred. If actual production is greater than budgeted production, the production volume variance is favorable. That is, the total fixed overhead has been allocated to a greater number of units, resulting in a lower production cost per unit.
The reason for this is that it provides for the more authentic allocation base, and the overheads are allocated properly this way. The technical variation in the normal costing and the standard costing is the use of costs for the costing purposes. This variation is what makes standard costing distinguished to the normal cost.
Managers can use these formulas to calculate the total production costs. For instance, managers first need to find out how many hours it took the company to produce the product and how much the company is paying its employees per hour.
Overhead volume variance, also called overhead efficiency variance, is the difference between the amount of overhead applied and the actual overhead applied. Overhead is all the product costs that a company incurs that aren’t part of direct labor or overhead. Wages paid to supervisors, janitorial staff, machine parts and machine maintenance are all common overhead costs. A business usually applies these overhead costs based on the number of labor hours incurred to create products. This rate is determined in advance then applied when actual labor hours are calculated.
This is beneficial when analyzing a specific portion of the production process and an exact accounting of costs is needed. Normal costing uses indirect materials and labor costs to estimate production costs. It provides a more consistent valuation of production costs which eliminates month to month fluctuations. Understanding how to calculate these costs, as well as the advantages of each, is important in choosing the appropriate methodology for a given production process. When actual production is lower than budgeted production, production volume variance is unfavorable.
A business measures its manufacturing and selling efficiency by examining any volume variances it incurs during production and sales. A volume variance is the difference between what a company expected to use and what it actually used.
Product
Sales volume variance is the difference between the quantity of inventory units the company expected to sell vs. the amount it actually sold. To calculate sales volume variance, subtract the budgeted quantity sold from the actual quantity sold and multiply by the standard selling price.