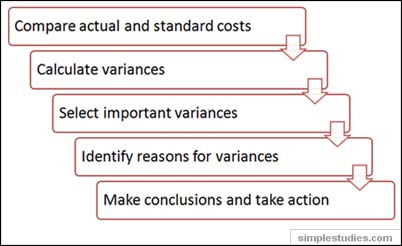
How to Calculate Sales Volume at Budgeted Mix
Read direct materials price and quantity standards article to understand how standard price and quantity of direct materials are set. Standard costs provide information that is useful in performance evaluation. Standard costs are compared to actual costs, and mathematical deviations between the two are termed variances.
How do you calculate sales quantity variance?
Sales Quantity Variance The variance is calculated by taking the difference between the actual sales volume at the budgeted mix and the budgeted sales volume and multiplying this by the budgeted price to give a monetary amount.
As an alternative for absorption costing the budgeted profit per unit or for marginal costing the budgeted contribution per unit can be substituted for the budgeted price in the above formulas. Before discussing sales mix and quantity variances it is first necessary clarify what is meant by the term ‘actual sales volume at budgeted sales mix’ and to understand how it is calculated. The actual cost less the actual quantity at standard price equals the direct materials price variance. The difference between the actual quantity at standard price and the standard cost is the direct materials quantity variance. The total of both variances equals the total direct materials variance.
Auto part suppliers that rely on steel will continue to scrutinize materials price variances and materials quantity variances to control costs, particularly in a period of rising steel prices. When actual quantity of materials used deviates from the standard quantity allowed to manufacture a certain number of units, materials quantity variance occurs. This is a variance of physical quantity but is also reported in dollars for proper financial measurement. To express this variance in dollars, both actual quantity used and standard quantity allowed are multiplied by standard price per unit of materials.
Favorable variances result when actual costs are less than standard costs, and vice versa. The following illustration is intended to demonstrate the very basic relationship between actual cost and standard cost. AQ means the “actual quantity” of input used to produce the output. AP means the “actual price” of the input used to produce the output. SQ and SP refer to the “standard” quantity and price that was anticipated.
The variance typically applies to direct materials in the manufacture of a product, but it could apply to anything – the number of hours of machine time used, square footage used, and so on. These thin margins are the reason auto suppliers examine direct materials variances so carefully. Any unexpected increase in steel prices will likely cause significant unfavorable materials price variances, which will lead to lower profits.
This means the company or the department is more profitable than expected. Quantity variances are important, but they are only one variance that managers study in a standard company variance analysis. The actual sales volume at budgeted mix is now calculated by applying these percentages to the actual total sales volume of the products.
Calculate the Budgeted Sales Mix Percentages
If actual volume is lower than actual volume at budgeted mix the formula will give a negative result and the sales mix variance is said to be unfavorable. For example, if the actual sales of the business are 10,000 units then the actual sales volume at budgeted sales mix is calculated as follows. The budgeted mix is simply the proportion by sales volume that each product represents of the total budgeted sales volume. For example if a business sells two products and budgets sales of product A of 9,000 units and product B of 3,000 then the budgeted sales mix percentage is calculated as follows.
Using this sales volume variance formula we can now show that the sales volume variance is equal to the sum of the sales mix and quantity variances. If the actual volume at budgeted mix is greater than the budgeted volume the sales quantity variance formula gives a positive result and the sales quantity variance is a favorable variance. If actual volume at budgeted sales mix is lower than budgeted volume the formula will give a negative result and the sales quantity variance is said to be unfavorable. The sales quantity variance shows how much of the sales volume variance was due to a difference between the actual volume sold at the budgeted mix and the budgeted volume. The variance is calculated by taking the difference between the actual sales volume and the actual sales volume at the budgeted mix and multiplying this by the budgeted price to give a monetary amount.
Using formulas to calculate direct materials variances
Variance analysis can be conducted for material, labor, and overhead. The difference between the standard cost of direct materials and the actual cost of direct materials that an organization uses for production is known as Material Cost Variance.
- Standard costs are used to establish the flexible budget for direct materials.
A total variance could be zero, resulting from favorable pricing that was wiped out by waste. A good manager would want to take corrective action, but would be unaware of the problem based on an overall budget versus actual comparison. In standard costing, the quantity variance could be the direct materials’ usage variance or the direct labor’s efficiency variance. The quantity variance is the difference between the quantity of inputs that were actually used versus the quantity of inputs that should have been used to manufacture the period’s output.
Note that there are several ways to perform the intrinsic variance calculations. One can compute the values for the red, blue, and green balls and note the differences. Or, one can perform the algebraic calculations for the price and quantity variances. Note that unfavorable variances (negative) offset favorable (positive) variances.
This is the difference between the standard and actual cost per unit of the direct materials purchased, multiplied by the standard number of units expected to be used in the production process. The sales volume variance is based on the difference between the actual volume of sales and the budgeted volume of sales multiplied by the budgeted unit price. If actual volume is greater than the actual volume at budgeted mix the sales mix formula gives a positive result and the sales mix variance is a favorable variance.
How do you find quantity variance?
A quantity variance is the difference between the actual usage of something and its expected usage. For example, if a standard quantity of 10 pounds of iron is needed to construct a widget, but 11 pounds are actually used, then there is a quantity variance of one pound of iron.
Sales Mix and Quantity Variances
Recall from Figure 10.1 “Standard Costs at Jerry’s Ice Cream” that the direct materials standard price for Jerry’s is $1 per pound, and the standard quantity of direct materials is 2 pounds per unit. Figure 10.4 “Direct Materials Variance Analysis for Jerry’s Ice Cream” shows how to calculate the materials price and quantity variances given the actual results and standards information. Review this figure carefully before moving on to the next section where these calculations are explained in detail. As we have seen, the total sales volume variance should equal the sum of the sales mix and quantity variances.
The sales mix variance shows how much of the sales volume variance was due to a difference between the actual sales mix and the budgeted sales mix. In a multi-product business the sales volume variance can be separated into sales mix and quantity variances. As you calculate variances, you should think through the variance to confirm whether it is favorable or unfavorable. For example, the materials price variance calculation presented previously shows the actual price paid for materials was $1.20 per pound and the standard price was $1. Clearly, this is unfavorable because the actual price was higher than the expected (budgeted) price.
Sales Quantity Variance
Because the company uses 30,000 pounds of paper rather than the 28,000-pound standard, it loses an additional $20,700. To compute the direct materials price variance, subtract the actual cost of direct materials ($297,000) from the actual quantity of direct materials at standard price ($310,500). This difference comes to a $13,500 favorable variance, meaning that the company saves $13,500 by buying direct materials for $9.90 rather than the original standard price of $10.35. A quantity variance is the difference between the actual usage of something and its expected usage. For example, if a standard quantity of 10 pounds of iron is needed to construct a widget, but 11 pounds are actually used, then there is a quantity variance of one pound of iron.
Angro Limited – a single product company – uses a perfect standard costing system. The normal wastage and inefficiencies are taken into account while setting direct materials price and quantity standards. Variances are calculated and reported at regular intervals to ensure the quick remedial actions against unfavorable situations. Managers use these variances between the actual cost and budgeted costs to plan future production and sales strategies. Many times production processes run smoother than anticipated and the actual costs are lower than the budgeted costs.
Standard costs are used to establish the flexible budget for direct materials. The flexible budget is compared to actual costs, and the difference is shown in the form of two variances. The materials quantity variance focuses on the quantity of materials used in production. It is defined as the difference between the actual quantity of materials used in production and budgeted materials that should have been used in production based on the standards. The above analysis uses the budgeted price per unit of the product to calculate the monetary value of the sales mix and quantity variances.