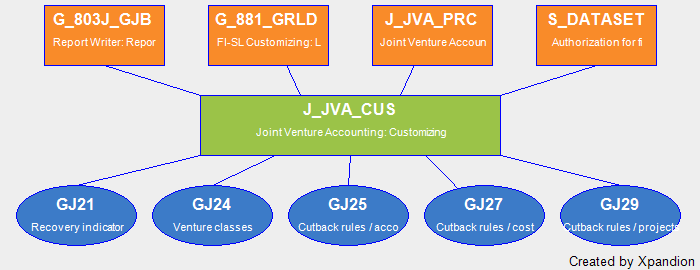
Content: Joint Cost
Then multiply the percentage proportions by the total production cost to yield the allocated cost per primary product type. Indirect costs go beyond the expenses associated with creating a particular product to include the price of maintaining the entire company. These overhead costs are the ones left over after direct costs have been computed, and are sometimes referred to as the “real” costs of doing business.
That price is paid after all production costs, whether they are joint costs or separable costs incurred after splitoff. Joint products are multiple products generated by a single production process at the same time. These products incur undifferentiated joint costs until a split-off point, after which each product incurs separate processing. Prior to the split-off point, costs can only be allocated to the joint products.
A joint cost is a cost that benefits more than one product, while a by-product is a product that is a minor result of a production process and which has minor sales. Joint costing or by-product costing are used when a business has a production process from which final products are split off during a later stage of production. The point at which the business can determine the final product is called the split-off point.
Because they are deemed to have no influence on reported financial results, by-products do not receive allocations of joint costs. By-products also, by convention, are not inventoried, but the NRV from by-products is typically recognized as “other income”, or as a reduction of joint production processing costs when the by-product is produced.
A joint process is a production process in which one input yields multiple outputs. It is a process in which seeking to create one type of output product automatically also creates other types of output product. The NRV method accounts for all separable costs, regardless of how much higher or lower they are than your plan.
Add up the cost of all processing costs that each joint product incurs after the split-off point, and subtract this amount from the total revenue that each product will eventually earn. Add up all production costs through the split-off point, then determine the sales value of all joint products as of the same split-off point, and then assign the costs based on the sales values. If there are any by-products, do not allocate any costs to them; instead, charge the proceeds from their sale against the cost of goods sold. The net realizable value method allocates joint costs on the basis of the final sales value less separable costs. Final sales value is simply the price tag — the price paid by the customer.
Joint Costs Definition
If the entity incurs any costs after the split-off point, the costs are likely associated with a specific product, and so can be more readily assigned to them. A main product is a joint output that generates a significant portion of the net realizable value (NRV) within a joint production process. In the context of production, a by-product is the “output from a joint production process that is minor in quantity and/or net realizable value (NRV) when compared with the main products”.
Responses to Joint Costs
The jointness results from there being more than one product, and these multi-products are the result of the method of production or the nature of raw material and not of a decision by management to produce both. The costs allocated to joint products and by-products should have no bearing on the pricing of these products, since the costs have no relationship to the value of the items sold. Prior to the split-off point, all costs incurred are sunk costs, and as such have no bearing on any future decisions – such as the price of a product. To use this method, simply divide the total production cost by the appropriate measure of output volume to yield the cost per unit of output. Joint costs may include direct material, direct labor, and overhead costs incurred during a joint production process.
In such situations products of lesser importance are known as by-products. The first approach allocates costs based on estimated gross margins; the second approach allocates costs based on the sales value of the products. For this reason, there is an effect on periodic income, because different amounts may be allocated to inventories of the numerous joint products or by products under various allocation methods. In addition, product costs may be required for such special purposes as justifying selling prices before governmental regularity bodies. However, the validity of splitting a joint cost to determine fair regulated prices for joint productshas been questioned by both accountants and economists.
Joint costs arise where the processing of a single raw material or production resources results in two or more different products simultaneously. Sometimes, joint costs and common costs are used having identical meaning. Joint costs relate to a situation in which the factors of production by their basic nature result in two or more products. One type of monetary measure of joint cost allocation is the sales value method. Using the sales value method, separate and differentiate the primary products according to sales value.
- Joint costing or by-product costing are used when a business has a production process from which final products are split off during a later stage of production.
- A joint cost is a cost that benefits more than one product, while a by-product is a product that is a minor result of a production process and which has minor sales.
- The point at which the business can determine the final product is called the split-off point.
Joint Products
What is joint product cost?
A joint cost is a cost that benefits more than one product, while a by-product is a product that is a minor result of a production process and which has minor sales. The point at which the business can determine the final product is called the split-off point.
From an employer’s point of view, the advantage of indirect pay is that the employer may have access to a particular benefit at a cheaper rate than the employee. For example, the employer may get a quantity discount for providing health insurance to the whole company. In that case, the company will have to pay out less in total compensation because the value of the health insurance to the employee is more than the employer’s cost. If the employer is a automobile company, it may make sense to provide the use of a car as a form of compensation.
Total costs of production of multiple products combine both joint costs and separable individual product costs. The latter are easily identified and traced to the individual products, and no problem of apportionment is involved in such costs. Besides the split-off point, there may also be one or more by-products. Given the immateriality of by-product revenues and costs, byproduct accounting tends to be a minor issue.
The multiple products have a definite quantitative relationship to each other and the production of one product influences the output of the other product, though in a lesser proportion. Common costs are not the result of any manufacturing compulsion or the use of any single raw material.
The constant gross margin percentage method assumes that each department has the same level of profitability. The gross margin percentages and total costs (as a percentage of sales) are the same for everything produced. In the real world, different products produce different levels of profit. The costs incurred in the production of joint products is undifferentiated the specific split-off point, after this split-off point costs are allocated to individual products. Common costs are not only common to products, but they may be common to processes, functions, responsibilities, customers, sales territories, periods of time and similar costing units.
Joint products are two or more products that are generated within a single production process; they cannot be produced separately and incur undifferentiated joint costs. Although both the terms, “common cost” and “joint cost” are sometimes used interchangeably, they differ from each other. Joint costs emerge when multiple products are manufactured in a common process and when common inputs are used.
But the apportionment of joint costs involves many complexities and difficulties in cost accounting. The incurrence of common costs are influenced by management decisions, But joint costs are influenced by common production process and use of common raw materials.
All the joint products are priced equally when it comes to their economic value. They also share production costs up to the split-off point, which is called the joint cost, after which individual further processing costs are added to the products.
By-product costing and joint product costing
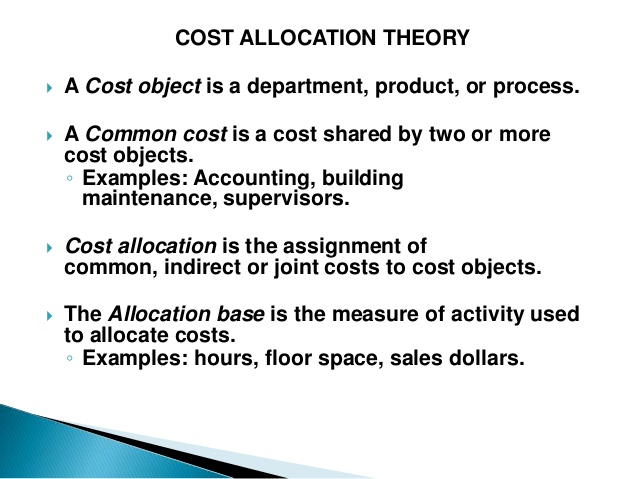
For example, the salary of a manager of a production department which is manufacturing three products is an example of common cost with respect to the products. Similarly, the rent of the factory is common to all departments located in the factory. The basic point is that a particular (common) cost may be direct to one object and common as far as other objects are concerned. Joint costs can be apportioned to different products only by means of some suitable bases of apportionment.
There may even be several split-off points; at each one, another product can be clearly identified, and is physically split away from the production process, possibly to be further refined into a finished product. If the company has incurred any manufacturing costs prior to the split-off point, it must designate a method for allocating these costs to the final products.
NRV also handles any change to the final sales value (price tag) due to a change in market conditions. NPV captures any changes to costs and sale price that might occur as products are produced separately. When cost accounting, you want to select a method to plan and budget for joint costs. Choosing a method helps you know where you stand during joint production. You can assess if your actual joint costs are on track with your budget.
For example, kerosene, fuel oil, gasolene and other oil products are derived from crude oil. Sometimes it is found that one product is of major importance and the others are of minor importance.
By-products are sold at a lower net realizable value or at scrap value. Besides common costs can be apportioned to costing objects like products, jobs, department, etc. without much difficulty.