Works-in-Progress vs. Finished Goods
These items are either just being fabricated or waiting for further processing in a queue or a buffer storage. This work in process formula yields an estimate, rather than an exact figure. It does not take into account added costs that may be incurred as work is completed, such as the cost of scrap, spoilage or the need to rework some items.
Work in progress, also referred to as WIP, is a term used in supply chain management to describe the costs of unfinished goods in the manufacturing process. Work-in-progress, as mentioned above, is sometimes used to refer toassetsthat require a considerable amount of time to complete, such as consulting or construction projects. This differentiation may not necessarily be the norm, so either term can be used to refer to unfinished products in most situations. This account of inventory, like the work-in-progress, may include direct labor, material, and manufacturing overhead.
Three general types of inventory control systems include continuous review systems, periodic review systems, and just-in-time inventory control. In the books, the company takes all costs associated with the WIP such as raw material cost, factory overhead cost, and direct labor costs and so on. WIP is clearly different from the other types of inventory for manufacturing concerns. Work in process (WIP), work in progress (WIP), goods in process, or in-process inventory are a company’s partially finished goods waiting for completion and eventual sale or the value of these items.
The three most important types of inventory are the raw materials, the work in progress (WIP) inventory and the finished goods. A term that many often use interchangeably with the WIP is the work in process. Though both terms mean the same, sometimes they may denote a different thing.
What is the difference between work in progress (WIP) and finished goods in accounting?
Ending WIP is listed on the company’s balance sheet along with amounts for raw materials and finished goods. Work in process or progress is a part of a manufacturing company’s current assets and its value needs included in the inventory-cost-of-production report.
Often, this is the case when the manufacturing operation is short enough to allow all work in process to be completed when the period ends and current accounts are closed. WIP is a concept used to describe the flow of manufacturing costs from one area of production to the next, and the balance in WIP represents all production costs incurred for partially completed goods. Production costs include raw materials, labor used in making goods, and allocated overhead.
Once you sell the finished goods, transfer the associated costs to the cost of goods sold account on the income statement. For most manufacturing operations, the costs that are included in an ending work in process inventory are raw materials or parts used, direct labor and manufacturing overhead. For construction or other lengthy projects, the components of a WIP are often listed as materials, wages and benefit costs for labor, subcontractor costs and expenses.
Costs that are represented in the work in progress account include direct materials, direct labor, and manufacturing overhead. As work proceeds in a production process, costs flow from the raw materials inventory account, into the work in progress inventory account, and then into the finished goods account. Represent all of these costs as current assets in inventory accounts on the balance sheet.
In accounting, a work in progress (WIP) account is an inventory account that includes goods that are in the process of being produced but are not yet finished. This account represents the costs of resources used but not yet turned into completed products. It is one of the inventory accounts commonly used to track the flow of costs in a production process. Other common inventory accounts include raw materials and finished goods.
Either way, determining the value of work in progress can be time consuming, so companies try to minimize the WIP directly before the end of the accounting period. Work in process is the term for a product that is being manufactured, but which is not yet completed. That is, WIP doesn’t include raw materials that have not been used yet or completed goods. Work in process inventory is an asset The ending work in process inventory is simply the cost of partially completed work as of the end of the accounting period.
Once these steps have been completed, the expenses can be divided by total units produced to obtain the cost per unit. Inventory is either the finished goods stored and offered for sale by a business or the raw materials used by a company to produce finished products. An inventory control system is a process businesses use to manage inventory.
A firm accounts for the work in progress towards the end of the accounting period. The accounting of WIP helps a company to determine the value of inventory that is in the production process.
Inventory accounts are reported as current assets on the company’s balance sheet. Use these accounts for internal analysis as well as external financial reporting. At any given time, a portion of the inventory in a manufacturing operation is in the process of being transformed from raw materials or components into finished goods. Refereed to as a work in progress, a work in process or a WIP, this part of the overall inventory is an asset. In order to properly account for partially completed work, a business needs to determine the ending work in process inventory at the end of each accounting period.
- In accounting, a work in progress (WIP) account is an inventory account that includes goods that are in the process of being produced but are not yet finished.
- It is one of the inventory accounts commonly used to track the flow of costs in a production process.
Work in progress inventory is more valuable than raw materialsthat have yet to be put into manufacturing use but is not more valuable than a company’s finished goods or finished inventory ready for sale. In essence, work in progress inventory is the middle stage of the production process between raw materials and the finished product. Inventory means those current assets, which have been or will be converted into the final products of a company for sale in the near future. In other words, inventory represents finished goods or goods in different stages of production that a company keeps at its premises or at third-party locations with ownership interest retained until goods are sold.
Understanding Works-in-Progress (WIP)
How do you calculate work in process inventory?
The work in process formula is the beginning work in process amount, plus manufacturing costs minus the cost of manufactured goods.
The WIP figure reflects only the value of those products in some intermediate production stage. This excludes the value of raw materials not yet incorporated into an item for sale. Work in progress also excludes the value of finished products held as inventory in anticipation of future sales.
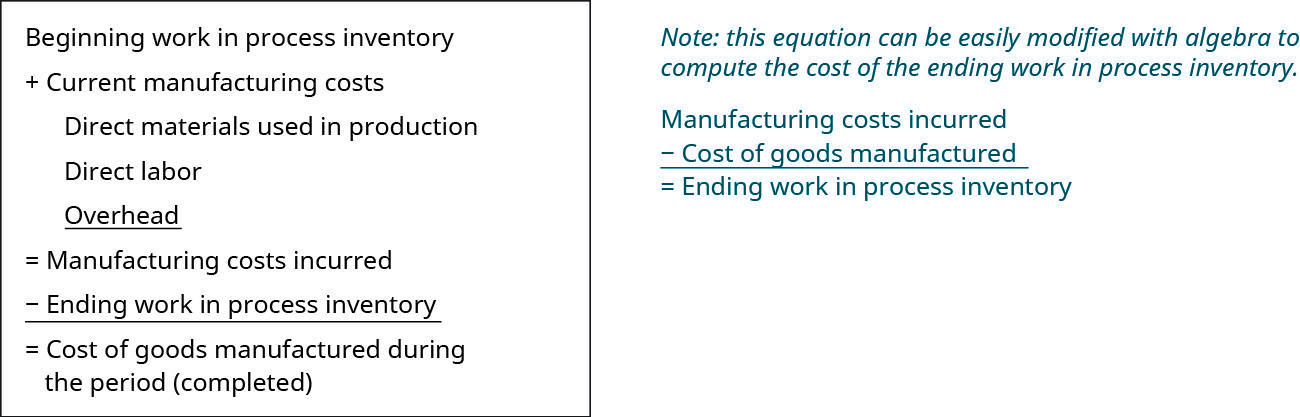
What is included in work in process inventory?
WIP refers to the raw materials, labor, and overhead costs incurred for products that are at various stages of the production process. WIP is a component of the inventory asset account on the balance sheet. These costs are subsequently transferred to the finished goods account and eventually to the cost of sales.
All costs associated with the work in progress inventory is taken into account, including raw materials cost, direct labor costs, and factory overhead costs. Direct materials are materials that are consumed during the manufacture of a product. To determine the cost per unit under process costing, each expense must first be assigned to a process then categorized as a direct materials cost or conversion cost.
Work in process is also a useful measure for management, because it provides a tool for tracking production flow and costs. The term work-in-progress (WIP) is a production and supply-chain management term describing partially finished goods awaiting completion. WIP refers to the raw materials, labor, and overhead costs incurred for products that are at various stages of the production process. WIP is a component of the inventory asset account on the balance sheet. These costs are subsequently transferred to the finished goods account and eventually to the cost of sales.
How to Calculate the Ending Work-in-Process Inventory
Work in progress is not accounted for in raw materials inventory and it is not ready for accounting as a final product. Small businesses need to consider the best way to valuate work-in-process inventory. Deciding how to account for work-in-process inventory value is an important financial accounting and strategic business decision. Companies must choose the best inventory valuation approach for accounting for these costs and must decide how to ultimately connect costs of work in process to costs added before the products become finalized. If work-in-process inventory is worth $10,000 and the final value of those products upon completion is $50,000, the additional $40,000 in production costs must be accounted for as the costs are added.
The work in process may sometime refer to a product that moves from raw materials to a finished product in a short time, such as manufacturing goods. On the other hand, the work in progress may refer to an asset that needs more time for completion, such as construction or consulting projects.
The WIP figure reflects only the value of those products in some intermediate production stages. The WIP figure also excludes the value of finished products being held as inventory in anticipation of future sales.
Manufacturing firms receive raw materials from suppliers, store them and maintain accounting for the value of the raw materials. As raw materials are pulled for use in production, they are no longer accounted for within materials inventory. Once products are finished, they are accounted for in the value of final product inventory. During the interim, the value of the work in process is accounted for separately. Beginning work-in-process inventory involves determining the value of products that are in production but that have not yet been completed at the end of an accounting period.