Although calculating overhead varies depending on the method used, there are three general types of expenses for manufacturing businesses. They consist of indirect materials, indirect labor and miscellaneous expenses. For service organizations, general and administrative expenses account for a large portion of overhead costs, and activity-based costing is one possible method for determining cost allocation. Regardless of the type of organization or accounting method used, knowing which expenses to allocate to overhead is important for financial reporting purposes. Since most of Boeing’s products are unique and costly, the company likely uses job costing to track costs associated with each product it manufactures.
Reasons for Overapplied Overhead
For example, overhead costs such as the rent for a factory allows workers to manufacture products which can then be sold for a profit. Overheads are also very important cost element along with direct materials and direct labor.
What is Underapplied overhead Overapplied overhead?
Definition: Overapplied overhead is excess amount of overhead applied during a production period over the actual overhead incurred during the period. In other words, it’s the amount that the estimated overhead exceeds the actual overhead incurred for a production period.
In accounting, all costs can be described as either fixed costs or variable costs. Variable costs are inventoriable costs – they are allocated to units of production and recorded in inventory accounts, such as cost of goods sold. Fixed costs, on the other hand, are all costs that are not inventoriable costs. All costs that do not fluctuate directly with production volume are fixed costs. Fixed costs include various indirect costs and fixed manufacturing overhead costs.
The overhead costs applied to jobs using a predetermined overhead rate are recorded as credits in the manufacturing overhead account. You saw an example of this earlier when $180 in overhead was applied to job 50 for Custom Furniture Company. The overhead is attributed to a product or service on the basis of direct labor hours, machine hours, direct labor cost etc. The overhead absorption rate is calculated to include the overhead in the cost of production of goods and services. It’s used to define the amount to be debited for indirect labor, material and other indirect expenses for production to the work in progress.
Sometimes the estimate is more than the actual amount and sometimes it’s less than the actual amount. Overapplied overhead happens when the estimated overhead that was allocated to jobs during the period is actually more than the actual overhead costs that were incurred during the production process. In a sense, the production managers came in “under budget” and achieved a lower overhead than the cost accountants estimated. For example, a business applies overhead to its products based on standard overhead application rate of $25 per hour of machine time used. Since the total amount of machine hours used in the accounting period was 5,000 hours, the company applied $125,000 of overhead to the units produced in that period.
Overhead expenses are all costs on the income statement except for direct labor, direct materials, and direct expenses. Overhead expenses include accounting fees, advertising, insurance, interest, legal fees, labor burden, rent, repairs, supplies, taxes, telephone bills, travel expenditures, and utilities.
Make a comprehensive list of indirect business expenses including items like rent, taxes, utilities, office equipment, factory maintenance etc. Direct expenses related to the production of goods and services, such as labor and raw materials, are not included in overhead costs. Note that all of the items in the list above pertain to the manufacturing function of the business. Rather, nonmanufacturing expenses are reported separately (as SG&A and interest expense) on the income statement during the accounting period in which they are incurred. For a product to be profitable, its selling price must be greater than the sum of the product cost (direct material, direct labor, and manufacturing overhead) plus the nonmanufacturing costs and expenses.
Therefore, overheads cannot be immediately associated with the products or services being offered, thus do not directly generate profits. However, overheads are still vital to business operations as they provide critical support for the business to carry out profit making activities.
Other examples of actual manufacturing overhead costs include factory utilities, machine maintenance, and factory supervisor salaries. All these costs are recorded as debits in the manufacturing overhead account when incurred. An allocation base should not only be linked to overhead costs; it should also be measurable. The three most common allocation bases—direct labor hours, direct labor costs, and machine hours—are relatively easy to measure. Direct labor hours and direct labor costs can be measured by using a timesheet, as discussed earlier, so using either of these as a base for allocating overhead is quite simple.
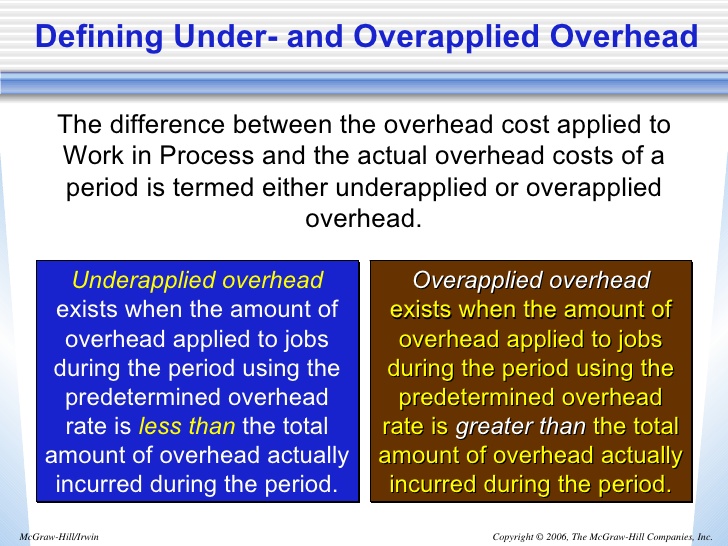
Thus there is a link between machine hours and overhead costs, and using machine hours as an allocation base is preferable. occurs when actual overhead costs (debits) are lower than overhead applied to jobs (credits). The T-account that follows provides an example of overapplied overhead. Note that the manufacturing overhead account has a credit balance when overhead is overapplied because more costs were applied to jobs than were actually incurred.
- They consist of indirect materials, indirect labor and miscellaneous expenses.
- Although calculating overhead varies depending on the method used, there are three general types of expenses for manufacturing businesses.
Here, overhead is estimated to include indirect materials ($50 worth of coffee), indirect labor ($150 worth of maintenance), and other product costs ($200 worth of rent), for a total of $400. It comprises of all indirect costs whether in the form of Indirect material, indirect Labor or Indirect Expenses which are incurred in the manufacturing of the goods and services. Overhead is overapplied because actual overhead costs are lower than overhead applied to jobs. If Chan’s production process is highly mechanized, overhead costs are likely driven by machine use.
Accounting Topics
For example, the costly direct materials that go into each jetliner produced are tracked using a job cost sheet. Direct labor and manufacturing overhead costs (think huge production facilities!) are also assigned to each jetliner. This careful tracking of production costs for each jetliner provides management with important cost information that is used to assess production efficiency and profitability. Management can answer questions, such as “How much did direct materials cost? ” This is important information when it comes time to negotiate the sales price of a jetliner with a potential buyer like United Airlines or Southwest Airlines.
Manufacturing overhead (also referred to as factory overhead, factory burden, and manufacturing support costs) refers to indirect factory-related costs that are incurred when a product is manufactured. In manufacturing, indirect materials include items that are used to produce a product that are not included in finished goods inventory.
Accountants, supervisors and other support services personnel that make production possible are categorized as indirect labor. It is important that management knows what it takes, administratively, to manufacture a product. However, support services can grow too large and reduce profit margins, which makes downsizing or labor reallocation necessary. Careful evaluation of indirect labor and its impact on overhead costs is needed to keep businesses operating efficiently and effectively. Chan Company estimates that annual manufacturing overhead costs will be $500,000.
The more direct labor hours worked, the higher the overhead costs incurred. Thus direct labor hours or direct labor costs would be used as the allocation base. If the department is expected to increase production in a particular month or quarter, and overhead costs are increased proportionately, this also could lead to overapplied overhead. The price of materials per unit may decrease as the department purchases more goods, which the manager may not have factored into her allocation of overhead funds.
occurs when actual overhead costs (debits) are higher than overhead applied to jobs (credits). The T-account that follows provides an example of underapplied overhead. Note that the manufacturing overhead account has a debit balance when overhead is underapplied because fewer costs were applied to jobs than were actually incurred. Remember that overhead applied does not represent actual overhead costs incurred by the job—nor does it represent direct labor or direct material costs. Instead, overhead applied represents a portion of estimated overhead costs that is assigned to a particular job.
Variable costs include direct labor, direct materials, and variable overhead. When this journal entry is recorded, we also record overhead applied on the appropriate job cost sheet, just as we did with direct materials and direct labor. Figure 2.6 “Overhead Applied for Custom Furniture Company’s Job 50” shows the manufacturing overhead applied based on the six hours worked by Tim Wallace. Notice that total manufacturing costs as of May 4 for job 50 are summarized at the bottom of the job cost sheet.
This can include items such as glue, staples, plastic wrap and tape used in the production process. Indirect materials vary widely given the nature of operations, but it is important they are included in the calculation of overhead costs. Management must know the true cost of producing a product, taking into account all of the inputs in the manufacturing process.
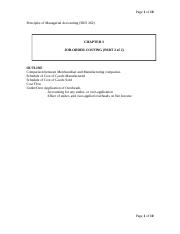
Machine hours can also be easily measured by placing an hour meter on each machine if one does not already exist. As their names indicate, direct material and direct labor costs are directly traceable to the products being manufactured. Manufacturing overhead, however, consists of indirect factory-related costs and as such must be divided up and allocated to each unit produced. For example, the property tax on a factory building is part of manufacturing overhead. This step requires adding indirect materials, indirect labor, and all other product costs not included in direct materials and direct labor.
In business, overhead or overhead expense refers to an ongoing expense of operating a business. Overheads are the expenditure which cannot be conveniently traced to or identified with any particular cost unit, unlike operating expenses such as raw material and labor.
Determine and Dispose of Underapplied or Overapplied Overhead
Chan allocates overhead to jobs based on machine hours, and it expects that 100,000 machine hours will be required for the year. Second, the manufacturing overhead account tracks overhead costs applied to jobs.
Likewise, production costs per unit often decrease when producing more goods. In other words, it costs less to produce a single product when a department is making 1,000 rather than 100. As with any estimation, the predetermined overhead rate isn’t always accurate.