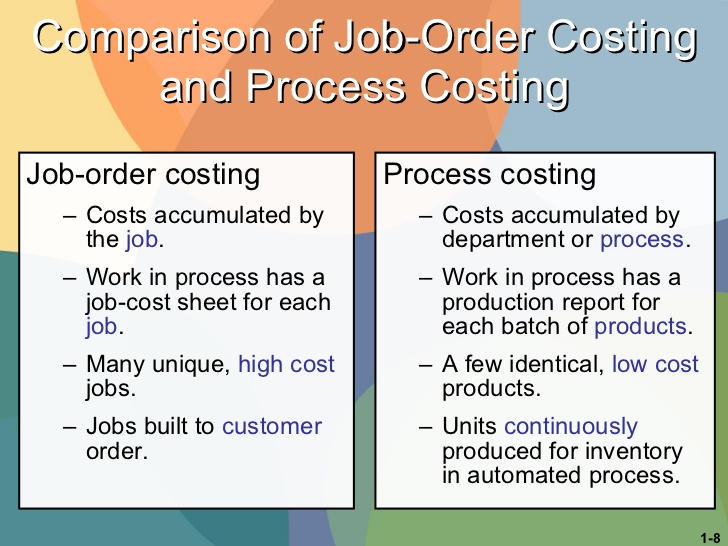
Comments on Job cost sheet
Again, there is no one single source of data that sets the cost standard. Job costing reports are management tools used to evaluate project or production performance against a known or estimated standard. They are used in many business sectors and their respective industries. The primary purpose of job costing reports is to identify discrepancies or beneficial results, usually in the form of financial values. They can be used to report both financial and numerical production outcomes.
It makes fewer assumptions than other costing methods. Manufacturing companies incorporate job order costing as a means of controlling usage of raw materials, production equipment and labor hours. These businesses consider each customer order a separate job for the purposes of job order costing. Alternatively, manufacturers may group smaller value projects together under a single job heading.
Job cost reports help the management team understand what drives the cost of the project and what particular underlying variables affected the results. Job cost reports identify production volume against time.
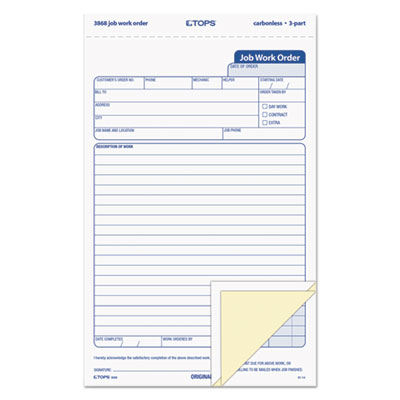
How are job order cost sheets used?
Job cost sheet. Job cost sheet is a document used to record manufacturing costs and is prepared by companies that use job-order costing system to compute and allocate costs to products and services. It is used as a subsidiary ledger to the work in process account because it contains all details about the job in process
Applied overhead is added to direct materials and direct labor to calculate total job cost. Many of these individual line items are developed over many years of learning about the respective subcontractors and suppliers. Imagine the detail related to the forms section of the estimate for concrete work in the first section above.
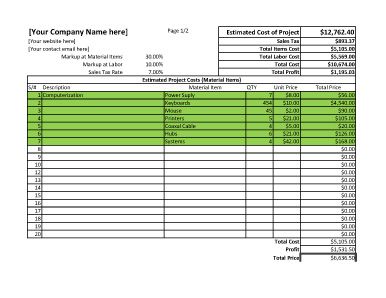
Job costing, also called project-based accounting, is the process of tracking costs and revenue for each individual project. Job costing looks at each project in detail, breaking down the costs of labor, materials and overhead.
Differences Process Costing Job Costing Product costs are assigned to departments (or processes). Unit Cost Information Similarities Unit cost information is needed by management for decision-making purposes. Differences Process Costing Job Costing Unit cost information comes from the departmental production cost report. Inventory Accounts Similarities Inventory accounts include raw materials inventory, work-in-process inventory, and finished goods inventory. Differences Process Costing Job Costing Several different work-in-process inventory accounts are used—one for each department (or process).
What is a job order cost sheet?
job order cost sheet definition. This is a record on an individual job (product, batch) within the job costing system. For items in process this is a subsidiary record to the general ledger account inventory: work-in-process (WIP).
All these costs that nickel and dime a project or manufacturing process are recorded and the company learns from the details. Adjustments are made for future estimates and the cycle continues.
Overhead is the most difficult cost to calculate, because you’ll need to rely on an approximation instead of a more exact figure. You’ll need to estimate the total overhead costs factoring into the job, including rent on your office, administrative costs and depreciation on the equipment used. Many businesses apply a blanket overhead fee to each project, such as 10 percent per job. An accountant can help you analyze your business and develop a specific approach to overhead. Or, you can calculate your predetermined overhead rate.
If volume decreases within a certain time frame, then management must address the underlying cause. Other reports identify the volume and waste associated with the raw materials, e.g. chocolate, sugar and nuts.
- In addition to helping management understand price changes, job cost reports help management evaluate performance.
- In manufacturing, job cost reports help identify the underlying issues that drive the overall final product cost higher.
The cost per unit is derived from the variable costs and fixed costs incurred by a production process, divided by the number of units produced. Examples of step costs are adding a new production facility or production equipment, adding a forklift, or adding a second or third shift. When a step cost is incurred, the total fixed cost will now incorporate the new step cost, which will increase the cost per unit. Depending on the size of the step cost increase, a manager may want to leave capacity where it is and instead outsource additional production, thereby avoiding the additional fixed cost. This is a prudent choice when the need for increased capacity is not clear.
Job costing is an accounting tool that allows businesses to track costs by individual jobs. Job costing is calculated by accumulating the cost of labor, materials and overhead for a specific project. The accounting department is responsible to record all manufacturing costs (direct materials, direct labor, and manufacturing overhead) on the job cost sheet. A separate job cost sheet is prepared for each individual job. Applied overhead is overhead added to a job by taking the predetermined overhead rate multiplied by theactual activity.
Job costing reports help management pinpoint which variable is driving the cost higher. The other direct costs on the job sheet use actual quantities and actual prices/rates. Product Costs Similarities Product costs consist of direct materials, direct labor, and manufacturing overhead.
When the reports are combined, the final actual cost of production per unit is compared against the standard. Development of cost standards come from multiple sources and variables. It is constantly changing and job costing reports help the contractor learn and improve performance.
K’s Premier Cabinets uses job costing to calculate the cost of jobs as they are completed. The company estimates that it will have $1,250,000 in overhead costs in 2015. The company believes that employees will work 200,000 hours and that 150,000 machine hours will be used during 2015. Calculate the predetermined overhead rate assuming that the company uses direct labor hours to allocate overhead to jobs.
The key to job costing reports is the value they bring with educating management about changes. When you subtotal the forms phase, estimated costs are $27,600, actual costs are $28,953. The total cost overrun of $1,353 is driven by the additional labor of $1,596. Did the job conditions change between the estimating period of time and actual time to do the work? Were there weather conditions that drove this cost overrun.
Cost Accounting For Dummies
In addition to helping management understand price changes, job cost reports help management evaluate performance. In manufacturing, job cost reports help identify the underlying issues that drive the overall final product cost higher. With manufacturing, product cost is driven by a certain volume over time given certain costs for raw resources and assuming certain waste factors.
I find it interesting that the cost for equipment was lower than estimated. Did the contractor use labor instead of equipment to get the work done? Was equipment available and ready to use during this phase? Notice how objective results can be influenced by subjective criteria (weather, availability, conditions etc.).
How to Calculate Job Costing
One work-in-process inventory account is used—job cost sheets track costs assigned to each job. Recall the three components of product costs—direct materials, direct labor, and manufacturing overhead. Assigning these product costs to individual products remains an important goal for process costing, just as with job costing. However, instead of assigning product costs to individual jobs (shown on a job cost sheet), process costing assigns these costs to departments (shown on a departmental production cost report).
job order cost sheet definition
Calculate how much it costs your business to employ all staff members who will work on the project per day. Multiply the payroll day rate by the amount of time you estimate you’ll need to complete the job. If you’ll rely on subcontractors for work your company doesn’t complete itself, factor those costs into your total labor costs for the job. It can help to get an estimate from each of these contractors.
Managerial accounting is very common with the manufacturing and construction industries. Managerial accounting’s primary concept is to compare the estimated cost against the actual cost.
Simply stated, a standard of cost is determined, then actual costs are calculated, the two are compared to identify discrepancies. One of the methods of managerial accounting is job costing. Job costing focuses on breaking down the project into phases or functions and comparing the estimated amounts for those phases/functions against actual costs.
The job used 45 direct labor hours and 30 machine hours. The average direct labor rate is $18.00 per hour and the company uses the predetermined overhead rate calculated in Example #1. It is easy to calculate the total cost of direct materials based on the materials used in the job. Companies usejob cost sheets to record the cost of materials used on the job.